Гидравлические системы играют важную роль во многих отраслях промышленности, обеспечивая высокую плотность мощности в компактных и эффективных корпусах. Однако традиционные методы субтрактивного производства ограничивают дизайн и производительность. Аддитивное производство предлагает решение, позволяя создавать сложные геометрические формы, улучшающие динамику потока, при этом минимизируя расход материалов. В этой статье Валерия Тирелли, генеральный директор Aidro Srl, рассказывает о том, как АМ меняет дизайн и производство гидравлических компонентов, предлагая новые возможности для повышения производительности, устойчивости и адаптации к конкретным условиям применения.
Гидравлические насосы, цилиндры и другие приводы обеспечивают большую мощность при меньших габаритах, чем двигатели, электромоторы и механические приводы. Гидравлические клапаны легко управляют направлением, скоростью, крутящим моментом и силой с помощью различных видов управления – от полностью ручного до управляемого сложной электроникой. Исторически сложилось так, что технологии производства этих гидравлических компонентов не успевали за расширяющимся спектром их применения. Появилось аддитивное производство металлов – набор промышленных процессов, предлагающих новые возможности для использования высокой плотности мощности гидравлических технологий путем улучшения проектирования и производства деталей гидросистем, таких как коллекторы, клапанные блоки и компоненты клапанов. По мере того как аддитивное производство продолжает набирать обороты в промышленности в целом, все большее число пользователей гидравлических систем уже получают выгоду от использования оптимизированных по весу и размеру гидравлических компонентов со сложными характеристиками, которые было бы сложно или невозможно изготовить с помощью традиционного производства. Это особенно актуально после того, как АМ преодолела трудности, связанные с очень высоким давлением, под которым работают гидравлические компоненты.
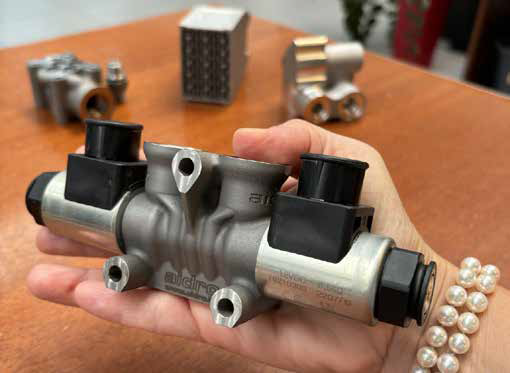
Рис. 1 По мере того как АП продолжает набирать обороты в промышленности, все большее число пользователей гидравлических компонентов внедряют эту технологию (предоставлено Aidro Srl)
Почему АП выгодно отличается от других способов производста
Аддитивное Производство предлагает иной подход к устоявшимся методам проектирования и изготовления гидравлических деталей. Вместо того чтобы начинать с металлического блока, процесс аддитивного производства позволяет инженерам и техническим дизайнерам проектировать гидравлические детали, основываясь на конкретных потребностях приложения, а не на ограничениях прошлых производственных процессов. Свободные от ограничений традиционной механической обработки, детали могут быть разработаны для наиболее эффективного сочетания производства и производительности, включая оптимизацию внутренних каналов для увеличения расхода и снижения падения давления. Кроме того, в течение нескольких часов можно изготовить множество различных прототипов, чтобы определить наилучшую конструкцию, прежде чем перейти к массовому производству, будь то традиционные или аддитивные методы. Эти компоненты могут быть изготовлены из различных материалов, включая нержавеющую сталь, алюминий и инконель, характеристики которых выгодно отличаются от кованых материалов. Действительно, многие материалы, обработанные методом АП, обладают лучшими механическими свойствами и плотностью, чем их литые аналоги. Хотя гидравлические компоненты могут быть изготовлены как традиционным способом, так и методом АП, традиционное производство неизбежно имеет недостатки. Как субтрактивный процесс, материал удаляется – обычно с помощью обработки на станках с ЧПУ – из более крупной детали, обычно металлической отливки или прутка, чтобы получить желаемую форму. Избыточный материал часто оставляют на месте, чтобы сэкономить на его удалении, в результате чего детали весят гораздо больше, чем нужно. Механическая обработка также ограничена в возможности изготовления некоторых конструкций. Проходы в обычных коллекторах часто должны быть расположены таким образом, чтобы предотвратить пересечение каналов, просверленных поперек, и обеспечить достаточное количество материала между каналами для обеспечения достаточной прочности. Кроме того, вспомогательные отверстия, просверленные для соединения внутренних проходов, должны быть заглушены, что создает возможность будущей утечки.
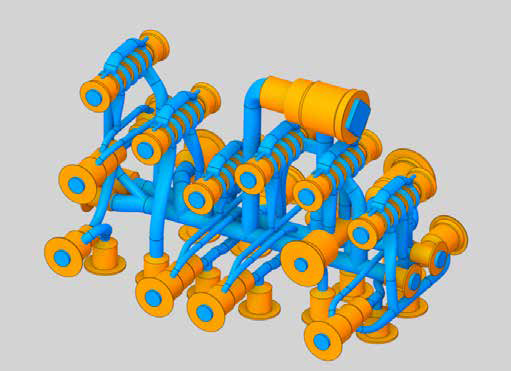
Рис. 2 Генеральный директор компании Aidro Валерия Тирелли с гидравлическим компонентом, изготовленным изготовленным методом аддитивного производства (PBF-LB) (предоставлено Aidro Srl)
«Освободившись от ограничений обычной механической обработки, можно спроектировать детали для наиболее эффективного сочетания производственных и эксплуатационных характеристик, включая оптимизацию внутренних каналов для увеличения расхода и снижения падения давления. Кроме того, можно изготовить множество различных прототипов в течение нескольких часов…»
Аддитивное производство, с другой стороны, «создает» желаемую деталь слой за слоем. С помощью этой технологии каналы потока могут быть размещены именно там, где они нужны, и оптимизированы по размеру и форме. До сих пор проточные каналы, особенно в таких компонентах, как клапаны, обычно были круглыми, поскольку их обрабатывали вращающимися фрезами. Послойная сборка компонентов позволяет разработчикам создавать конфигурации, которые было бы сложно или невозможно использовать при субтрактивных методах производства. Проточные каналы коллекторов теперь можно изготавливать с поперечным сечением и специальной формой вместо круглого отверстия, что позволяет оптимизировать пропускную способность канала той же (или меньшей) ширины, а иногда и на меньшей площади. Поскольку проходы, соединяющие внутренние каналы, не нужно обрабатывать снаружи коллектора, отпадает необходимость в заглушках для отверстий. Хотя существует большое разнообразие процессов аддитивного производства, в этой статье речь пойдет о технологии Laser BeAM Powder Bed Fusion (PBF-LB), при которой металлический порошок послойно расплавляется с помощью лазера. Другие процессы, используемые для изготовления гидравлических компонентов, включают струйное напыление связующего (BJT), при котором частицы порошка удерживаются вместе связующим веществом перед спеканием. В обоих случаях материал добавляется только там, где это необходимо. Это позволяет производителям создавать новые, легкие конструкции с различной геометрией и уменьшенным количеством деталей. Вместо того чтобы собирать три или четыре компонента (например, клапаны и коллекторы), можно сконструировать одну деталь, включающую эти компоненты. Это обеспечивает снижение веса, исключает сборочные операции, снижает риск утечки при соединении нескольких деталей и сокращает время обработки.
«Аддитивное производство, с другой стороны, «создает» желаемую деталь слой за слоем. С помощью этой технологии проточные каналы можно разместить именно там, где они нужны, и оптимизировать их размер и форму».
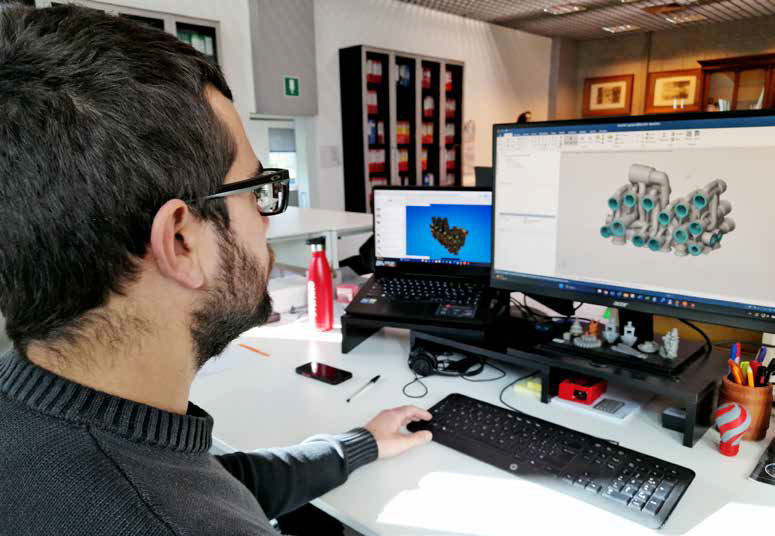
Рис. 3 Именно на этапе проектирования можно придать компоненту, изготовленному аддитивным способом, значительную ценность (Предоставлено Aidro Srl)
Обеспечение устойчивости как при производстве, так и при использовании
Во многих случаях аддитивное производство обеспечивает значительные преимущества с точки зрения устойчивости. Процессы АП требуют значительно меньше материала, чем субтрактивные процессы, такие как обработка на станках с ЧПУ, которые обязательно должны начинаться с большего количества материала, чем требуется для конечного компонента. Также было продемонстрировано снижение энергопотребления при сравнении ковки или литья с аддитивным производством. Создание легких деталей с помощью АП также способствует достижению целей устойчивого развития конечных пользователей. Транспортные средства или мобильная техника, в которые устанавливаются облегченные детали, могут выиграть от повышения топливной эффективности, поскольку использование облегченных компонентов снижает общий вес транспортного средства и, следовательно, расход топлива. Это особенно полезно в аэронавтике и космической отрасли, где каждый грамм, сэкономленный на компонентах, означает не только снижение воздействия на окружающую среду, но и значительную экономию средств.

Рис. 4 Изображение гидравлического коллектора UGO, используемого на зерноуборочных комбайнах (предоставлено Aidro Srl)
Пример из практики: коллектор UGO
Интересным примером из области сельскохозяйственного оборудования является гидравлический коллектор, показанный на рис. 4. Разработанный компанией Aidro, UGO является прекрасным примером коллектора, изготовленного аддитивным способом, который демонстрирует преимущества этой технологии для жидкостных силовых систем.
Коллектор UGO – это система, с помощью которой осуществляется управление зерноуборочными комбайнами. Он работает на гидравлических цилиндрах и моторах и традиционно состоит из:
- Шесть клапанов управления направлением
- Четыре редукционных клапана
- Один клапан сброса давления
- Один байпас
- Два обратных клапана с пилотным управлением

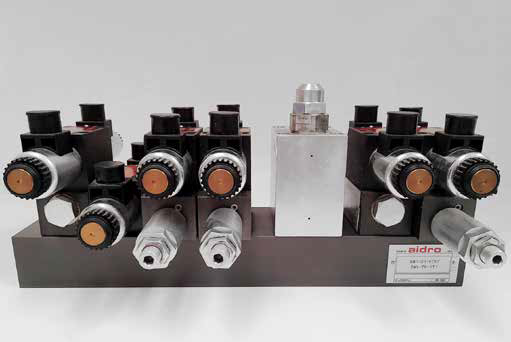
Рис. 5 Коллектор, изготовленный аддитивным способом (вверху), выполняет те же функции, что и оригинальный блок, который он заменяет (внизу), но имеет вдвое меньший размер. функции, что и оригинальный блок, который он заменяет (внизу), но при этом он вдвое меньше по размеру и (любезно предоставлено компанией Aidro Srl)
Коллектор, изготовленный методом аддитивного производства, выполняет те же функции, что и оригинальный блок, который он заменяет, но при этом имеет вдвое меньшие размеры и вес (рис. 5). В то время как традиционный коллектор изготавливается из нескольких материалов (алюминий для основания, чугун и сталь для клапанов), новая конструкция полностью выполнена из нержавеющей стали 316L. Этот материал сочетает в себе отличную прочность, высокую пластичность и хорошие термические свойства, что, наряду с высокой устойчивостью к коррозии и точечной коррозии (в том числе химической), делает его особенно подходящим для машин, используемых в сельском хозяйстве. 316L также лучше противостоит атмосферным агентам и химическим продуктам, используемым в этом секторе. Испытания под давлением аддитивно изготовленного 316L также показали, что механические свойства – такие как прочность на разрыв, удлинение, ударная вязкость и твердость – не хуже, а то и лучше, чем у обычных материалов через какие комбайны.
Сравнение традиционного производства с аддитивным производством сборного коллектора | |||
Параметр | Классическая технология | Аддитивное производство | Комментарии |
Масса | 23,3 кг | 11,3 кг | Обе массы включат клапана |
Количество деталей | 194 | 42 | Снижение веса в основном за счет удаления винтов, прокладок, крышек |
Материал | Алюминий для коллектора и чугун/сталь для клапанов | Сталь 316L | |
Рабочее давление | 250 бар | 250 бар | 250 бар – это то, что требуется для данного приложения, хотя коллекторы AM могут без проблем выдерживать и более высокое давление; однако максимальное давление клапанов составляет 350 бар. |
Таблица 1 Сравнение оригинальных и аддитивно-изготовленных коллекторов (предоставлено Aidro Srl)
«Во многих случаях аддитивное производство обеспечивает значительные преимущества с точки зрения устойчивости. Процессы АП требуют значительно меньше материала, чем субтрактивные процессы, такие как обработка с ЧПУ, которые обязательно должны начинаться с большего количества материала, чем требуется для конечного компонента.»
Как уже отмечалось ранее, одним из преимуществ внедрения аддитивного производства является возможность объединения нескольких деталей в одну, что сокращает время сборки и упрощает цепочку поставок. В случае с коллектором UGO оригинал состоял из 194 деталей, включая тринадцать основных блоков, двенадцать блоков корпуса клапана, один базовый коллектор и множество мелких компонентов, таких как золотники, уплотнительные кольца, винты, прокладки и крышки. Версия коллектора АП состоит всего из сорока двух деталей, включая один центральный блок.
Эффективность

Рис. 6 Детальный вид коллектора UGO (предоставлено Aidro Srl)
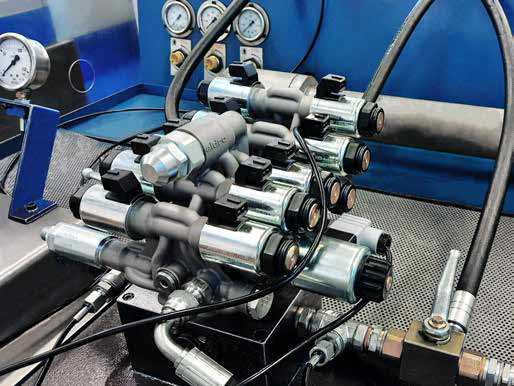
Рис. 7 Испытание коллектора UGO в условиях эксплуатации (предоставлено
Aidro Srl)
Эксплуатационные характеристики коллектора UGO превосходят характеристики оригинальной детали, поскольку изогнутая форма внутренних каналов означает отсутствие углов 90° в местах пересечения (рис. 6). Кроме того, как уже упоминалось выше, проходы, соединяющие два или более внутренних канала, не нужно обрабатывать снаружи коллектора и впоследствии закупоривать, чтобы предотвратить вытекание жидкости. Действительно, при традиционном производстве гидравлических систем пересечения коллекторов создаются путем сверления отверстия с одной стороны и другого отверстия с другой стороны блока, что является результатом ограничений, накладываемых станками. Освободившись от этих ограничений, инженеры могут проектировать компоненты на основе принципов вычислительной гидродинамики. Возможность аддитивного производства оптимизированных изогнутых каналов позволяет улучшить динамику потока и снизить перепады давления. Это, в сочетании с устранением риска утечки за счет отказа от вспомогательных крышек и заглушек, дает двойное преимущество: оптимизируются эксплуатационные характеристики и снижается риск нанесения ущерба окружающей среде. Более того, свобода проектирования, которую дает аддитивное производство, позволяет инженерам размещать проточные каналы именно там, где они необходимы, причем самых разных форм и размеров. Это означает, что каналы могут быть расположены ближе друг к другу, чем в обычных коллекторах, что делает готовые изделия более компактными и легкими. В данном примере коллектор АП UGO на 50 % меньше исходного компонента. Уменьшение размеров компонентов, достигаемое с помощью АП, особенно ценно, когда детали предназначены для мобильного применения и имеют сравнительно небольшое пространство для размещения гидравлических систем. Форма коллектора UGO была адаптирована к имеющемуся пространству, а соединения подобраны точно к месту подвода внешних трубопроводов. Это означает, что коллектор не нуждается в модификации после производства, поскольку он разработан именно для своего уникального применения.
Заключение
Аддитивное производство представляет собой трансформационный сдвиг в проектировании и производстве гидравлических компонентов. Освобождая инженеров от ограничений традиционного производства, АМ позволяет создавать более легкие и эффективные детали с оптимизированной динамикой потока и улучшенными характеристиками. На примере коллектора UGO показано, как АМ позволяет значительно уменьшить размер и вес компонентов, упростить сборку и повысить надежность за счет исключения элементов, склонных к поломкам, таких как вспомогательные заглушки. Помимо производительности, преимущества АМ с точки зрения экологичности, включая снижение расхода материалов и энергопотребления, соответствуют растущему вниманию к экологически ответственному производству. По мере развития технологии она будет играть все более важную роль в секторе жидкостных систем, стимулируя инновации и удовлетворяя разнообразные требования современных приложений.
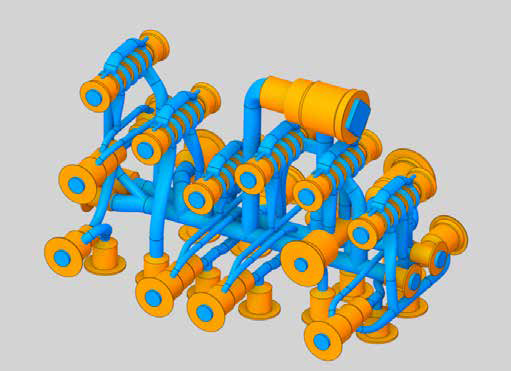
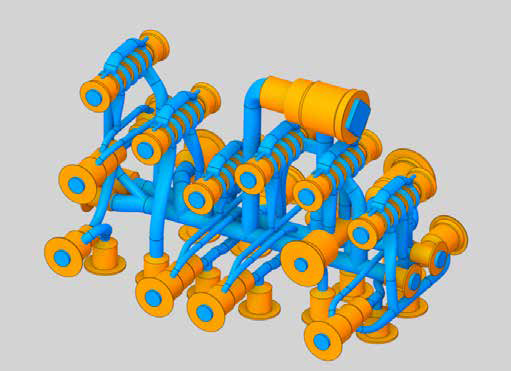
Рис. 8 Оригинальный коллектор (вверху) состоит из 194 деталей, включая тринадцать основных блоков, двенадцать блоков клапанных корпусов, один базовый коллектор и множество мелких компонентов, таких как золотники, уплотнительные кольца, винты, прокладки и крышки. Коллектор AM (вверху) состоит всего из сорока двух деталей, включая один центральный блок, и имеет значительно улучшенные характеристики благодаря оптимизированной конструкции каналов (Предоставлено Aidro Srl)
«Освобождая инженеров от ограничений традиционного производства, АП позволяет создавать более легкие и эффективные детали с оптимизированной динамикой потока и улучшенными характеристиками».