Мы часто слышим вопрос от заводских управленцев самого разного уровня, от начальников цехов и отделов до топ-менеджеров, включая генеральных директоров: «У нас серийное производство. Мы полностью задействовали все возможные ресурсы по управлению предприятием и с некоторых пор уперлись в потолок в плане производительности, качества, гибкости, конкурентоспособности. Помогут ли нам аддитивные технологии (АТ) выйти на новый уровень?».
Если бы этот вопрос обсуждался в какой-нибудь профильной группе в социальных сетях, мы уверены, что поток предложений был бы огромным. Однако далеко не все из них реально решали бы проблемы заказчика. Чаще всего это было бы перечисление ассортимента продуктов и материалов от разных компаний-разработчиков. В результате у задавших вопрос могло бы сложиться впечатление, что АТ у нас активно развиваются: есть множество производителей оборудования, программного обеспечения и компаний, предлагающих услуги для «чудесного преображения» производственного процесса.
От обилия таких предложений может возникнуть ощущение, что мир уже давно ушёл вперёд, а вы по какой-то причине всё ещё используете устаревшие подходы из «эпохи динозавров». Однако мало кто готов дать гарантию, что внедрение конкретной инновации действительно решит текущие задачи вашего предприятия.
В итоге компании зачастую всё же принимают решение о покупке оборудования для аддитивного производства (АП). И часто разочаровываются по причине не рационального подбора технологии и оборудования, спонтанности, отсутствия квалифицированного персонала с достаточным опытом проектирования, работы и обслуживания оборудования, а также быстрого устаревания 3D-принтеров, на смену которым уже через полгода может прийти новые модели, а то и технологии с гораздо более высокими характеристиками.
Но важно понимать: это оборудование не начнёт сразу выпускать серийную продукцию. Чтобы это произошло, требуется время и серьёзная работа по интеграции технологий в существующие производственные процессы, адаптации персонала и налаживанию новых цепочек поставок.
То, что игнорировать прогресс нерационально, понятно каждому здравомыслящему предпринимателю, акционеру и управленцу. Но насколько АТ стали «своими» для промышленников, придерживающихся проверенных временем методов? Здесь возникает принципиальный вопрос, заставляющий задуматься: что на самом деле нужно современному промышленнику?
Крупные компании выбирают технологии и оборудование, которые обеспечивают надёжность, производительность и оптимальное соотношение затрат и эффективности. Одни из них ориентируются на максимальную выработку на одного сотрудника (не сокращая персонал) или на каждый квадратный метр производственной площади. Другие же стремятся к полной автоматизации процессов с минимизацией человеческого фактора благодаря сложно перенастраиваемой производственной конвейерной линии или находящейся в тренде гуманоидной робототехники. В обоих случаях без внедрения инноваций не обойтись.
Аддитивное производство может стать одной из таких инноваций. Оно способно частично решить задачи заказчика, особенно в сочетании с классическими методами (гибридный подход). Однако, несмотря на потенциал 3D-печати, в России пока мало успешных примеров применения для серийного производства. За рубежом таких примеров тоже немного, но они наглядно показывают, что при твёрдом целеполагании и визионерских способностях руководства или любого инициативного лидера проекты могут стать знаковыми для всей индустрии.
Вот лишь некоторые из них:
- Форсунка для двигателей CFM International LEAP 1A и 1B, разработанная совместным предприятием компаний GE Aviation (ныне GE Aerospace) и Safran Aircraft Engines, была произведена в количестве сотен тысяч единиц. В каждом двигателе используется 18 или 19 топливных форсунок, изготовленных методом АП с использованием технологии селективного лазерного плавления СЛП/L-PBF. Двигатели используются на авиалайнерах Airbus A220, A320neo, A321neo, Boeing 737 MAX и COMAC C919. Эта форсунка приобрела популярность благодаря агрегации 20 деталей в одну, что позволило снизить вес на 25% и повысить топливную экономию до 15% по сравнению с предыдущими моделями двигателей, такими как CFM56. Кроме того, прочность детали увеличилась в 5 раз благодаря использованию кобальто-хромового сплава и оптимизации конструкции, а также обеспечению устойчивости к высоким температурам до 2400 °C. Одним из самых значимых результатов для руководства компании стало снижение затрат на материалы и упрощение производственного процесса, что позволяет экономить до 3 миллионов долларов на каждом самолете. В 2021 году сообщалось, что детали успешно налетали более 10 миллионов часов.
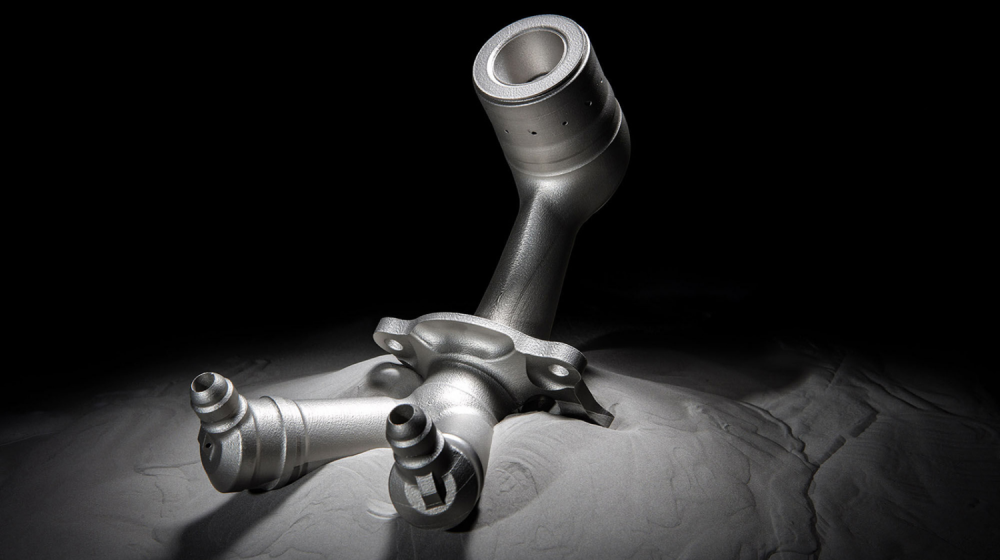
Рис. Напечатанная топливная форсунка (GE Aerospace)
- ECCO, в сотрудничестве со Stratasys и Henkel-Loctite, внедрила фотополимерную 3D-печать для создания форм, используемых в разработке и производстве уникальных подошв для своей обуви. Совместная разработка позволила создавать формы, выдерживающие более 1000 циклов впрыска без признаков износа. Новая технология обеспечивает значительное снижение затрат и ускорение процесса разработки по сравнению с традиционными алюминиевыми формами. Несмотря на то, что здесь мы говорим о печати единичной формы, она дает возможность также осуществлять серийное производство, избавляя от необходимости задействования инструментального производства.
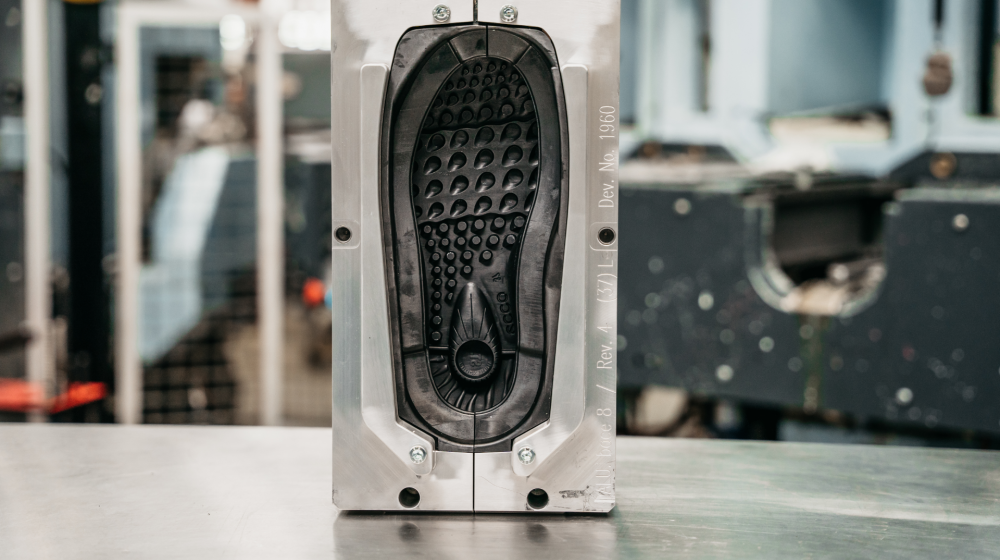
Рис. Индивидуализированная фотополимерная вставка в обувную пресс-форму (BUSINESS WIRE)
- Компания Merit3D напечатала для Adhesive Technology 1 миллион кронштейнов для крепления смесительной насадки к тюбику с эпоксидной смолой. Особенностью проекта явился вынужденный уход от затрудненной логистики с Китаем во время ковидных ограничений. Инженеры используют фотополимерную технологию LCD, материал от BASF, что позволяет обходиться без оснастки, менять форму кронштейнов и даже материал при любых новых обстоятельствах.
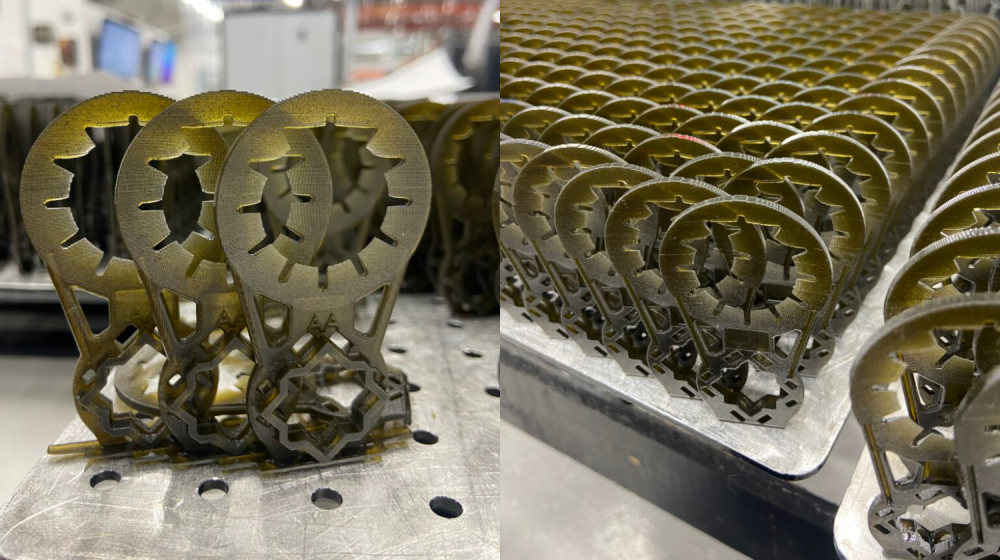
Рис. Серийное производство кронштейнов для крепления смесительной насадки (Merit3D)
- Компания GE Additive произвела более 100 000 напечатанных ацетабулярных чаш для тазобедренных суставов по технологии электронно-лучевой плавки ЭЛП/E-PBF с 2007 по 2018 год. Технология ЭЛП предлагает множество преимуществ для производства многих медицинских имплантатов. Она обеспечивает высокую прочность и точность изделий, свободу проектирования и снижение стоимости производства вплоть до 50%, что делает ее предпочтительным выбором по сравнению с традиционными методами производства в области медицины и других высокотехнологичных отраслей.
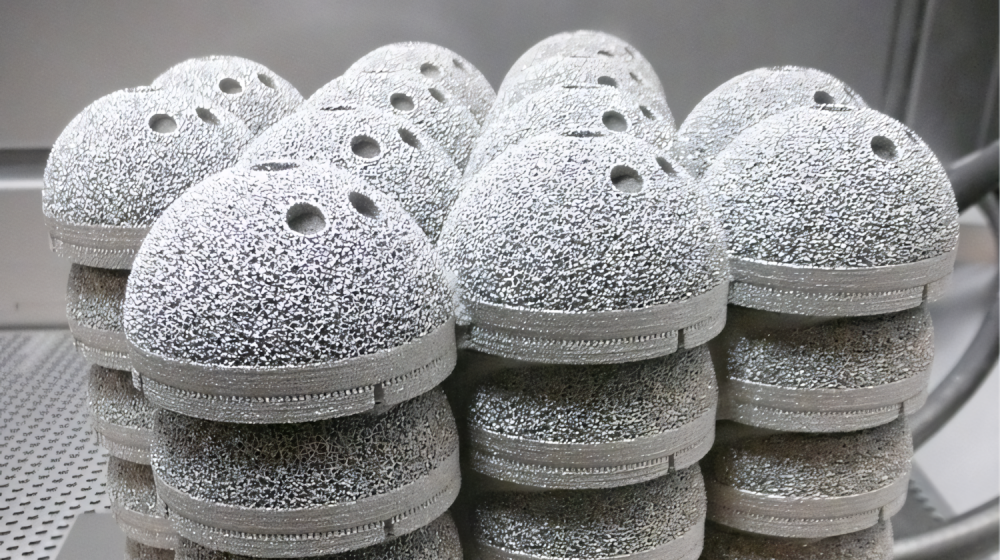
Рис. Производство ацетабулярных чаш по технологии ЭЛП (GE)
- Проект Michelin по производству металлических ламелей с использованием 3D-печати начался в 2017 году и успешно продолжается до сих пор. Ежегодно производится один миллион ламелей для пресс-форм шинной продукции. В результате скорость производства партии сократилась с недель до дней, отходы материала снизились на 20%, а затраты на производство – на 30-50%, увеличилась производительность и эффективность шин на дорогах благодаря производству ламелей с индивидуальными характеристиками, срок службы шин увеличился на 10-15%.
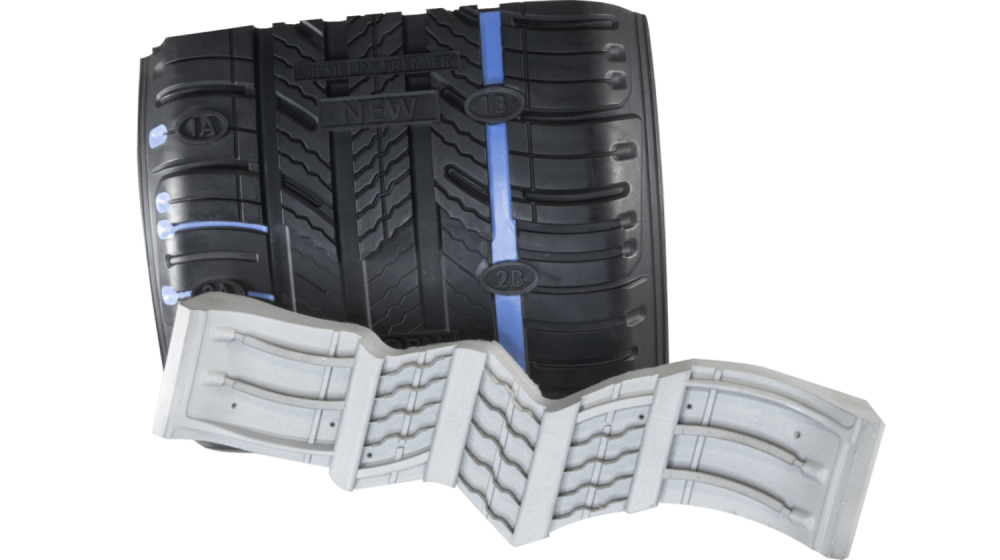
Рис. Пресс-форма с ламелями и готовая шинная продукция (AddUp)
Не правда ли, такие примеры способны подвигнуть многих промышленников пересмотреть их отношение к 3D-печати и поставить его на один уровень с классическим производством? Почему же достоинства АТ часто недооцениваются? Одна из причин — поверхностное восприятие АП, вызванное недостаточной осведомлённостью о его возможностях, а также ошибками интеграторов и производителей.
Мы неслучайно начали с ярких примеров, чтобы уже в начале статьи помочь читателю открыть для себя новые перспективы. Возникает вопрос: хватит ли сил, знаний, опыта, времени и инвестиций для реализации таких проектов у тандема «классических» промышленников и организаций, работающих в сфере АП? Этот вопрос в России поднимается нечасто.
Тем не менее, примеры серийного производства в мире с использованием 3D-печати существуют, и они далеко не единичны.
Для многих отечественных промышленников важнее всего видеть примеры, реализованные в России, а не за рубежом. Это логично: в условиях санкций предприятия вынуждены работать с отечественными партнёрами. Если у таких компаний нет опыта в подобных проектах, то становиться первопроходцем и сталкиваться с трудностями готовы далеко не все.
Отечественный опыт успешного внедрения АТ уже есть, и эти примеры могут стать ориентиром для тех, кто готов сделать шаг вперёд и использовать 3D-печать для выхода на новый уровень.
Почему серийное производство с использованием 3D-печати пока не стало массовым в России? Несмотря на глобальный интерес к АТ, в России их серийное применение остается скорее исключением, чем правилом. Основная причина кроется в незрелости отечественного рынка. Да, можно найти отдельные успешные примеры внедрения, однако они лишь подчеркивают ограниченность и фрагментарность развития данной отрасли. Даже на мировом уровне зрелость АТ остается дискуссионной темой: она во многом зависит от отрасли, географии и уровня технологического развития.
Готова ли Россия к массовому внедрению промышленного АП? Ответ – «да», но с оговорками. На сегодняшний день применение АТ в нашей стране остается избирательным и сосредоточено лишь в нескольких ключевых секторах: авиация, космонавтика, медицина (хирургия, стоматология, протезирование), оборонно-промышленный комплекс (ОПК). Также наблюдаются первые попытки интеграции АТ в топливную отрасль. Однако эти примеры скорее демонстрируют усилия по освоению технологий, чем их широкую доступность и масштабируемость.
Основными барьерами в этом можно назвать:
- Ограниченный доступ к передовым технологиям. Российские инженеры долгое время полагались на копирование лучших зарубежных решений. Однако с учетом современных геополитических условий и ограничений в доступе к западным инновациям, отечественная отрасль оказалась в изоляции, что замедляет ее развитие.
- Низкая готовность производственного бизнеса. Многие компании видят в АТ перспективы, но не всегда готовы вкладываться в дорогостоящие системы, срок устаревания которых может составить менее 3 лет. На мировом рынке это понимание уже привело к выборочному подходу: покупают системы, которые обеспечивают измеримую эффективность, часто в нишевых, но прибыльных применениях.
Чему учит зарубежный опыт? На Западе компании, которые используют АТ в серийном производстве, демонстрируют определенные успехи. Хотя лишь немногие предприятия вышли на плато их промышленного использования, инвестиции в высокопроизводительные системы дают бизнесу ощутимую отдачу. Это подталкивает компании к долгосрочному планированию и закладке бюджетов на модернизацию оборудования.
Для российского рынка урок очевиден: успех АТ напрямую связан с созданием устойчивой экосистемы – от доступных разработок и материалов до качественного сервисного обслуживания. Это требует системных инвестиций, грамотной стратегии и активного международного сотрудничества. Без этого серийное производство с применением 3D-печати так и останется точечной практикой, а не массовым явлением.
Например, сегодня технология селективного лазерного плавления L-PBF/SLM считается одной из самых зрелых для коммерческого применения. Это подтверждается использованием принтеров с большими рабочими зонами (свыше 1 метра по одной из сторон), высокой производительностью (от 4 до 64 лазеров) и активным внедрением в авиационной и медицинской отраслях, а также в ОПК.
Но представьте себе технологии, которые способны значительно повысить производительность даже уже зрелых решений при минимальных инвестициях. Такой прорыв неизбежно вызовет резонанс и откроет новые горизонты для промышленности.
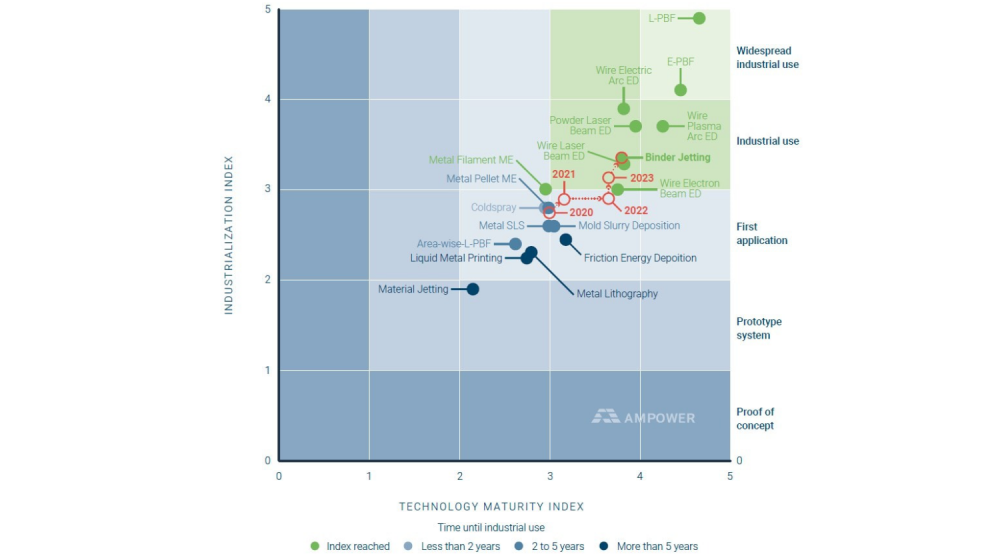
Рис. Диаграмма технологической зрелости АТ по металлу (Ampower, 2024)
Подобные технологии нового поколения, например, по работе с металлами и сплавами, находятся на пороге значительных изменений. Уже в ближайшее время они могут устранить ключевые недостатки существующих методов, таких как лазерное и электронно-лучевое плавление (L-PBF/E-PBF).
Одним из наиболее перспективных направлений является лазерная технология Area Printing, разработанная Seurat Technologies. Она представляет собой кардинальный апгрейд лазерного плавления, позволяя заменить десятки традиционных 3D-принтеров одной установкой. Это решение сочетает высокую производительность с возможностью точного масштабирования.
Еще одна инновация — безлазерная технология Metal Binder Jetting (MBJ/BJT), которая предлагает совершенно иной подход к работе с металлами. Вместо использования лазеров или электронных пучков, процесс основан на связующем веществе, что позволяет сократить затраты на оборудование и повысить производительность.
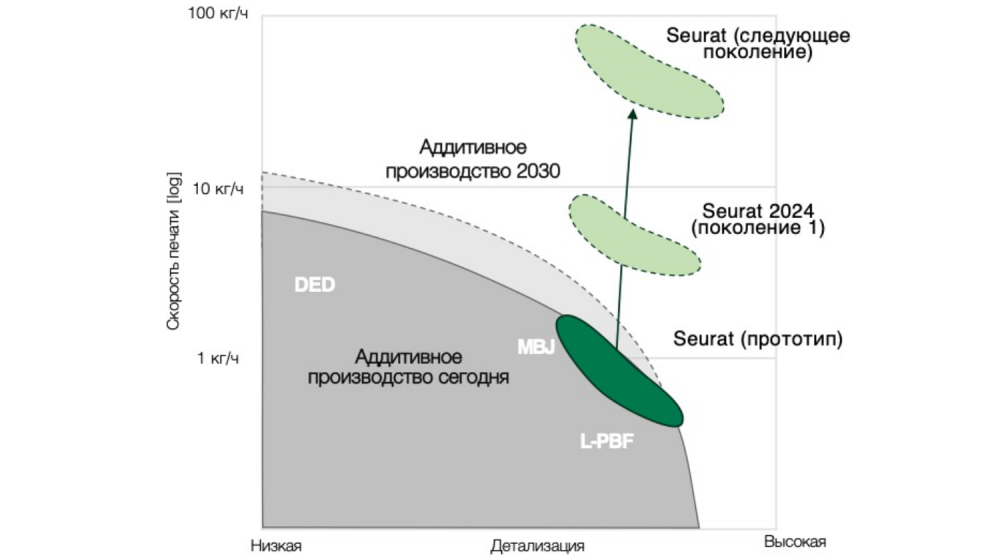
Рис. Перспективы развития технологии Area Printing (Seurat)
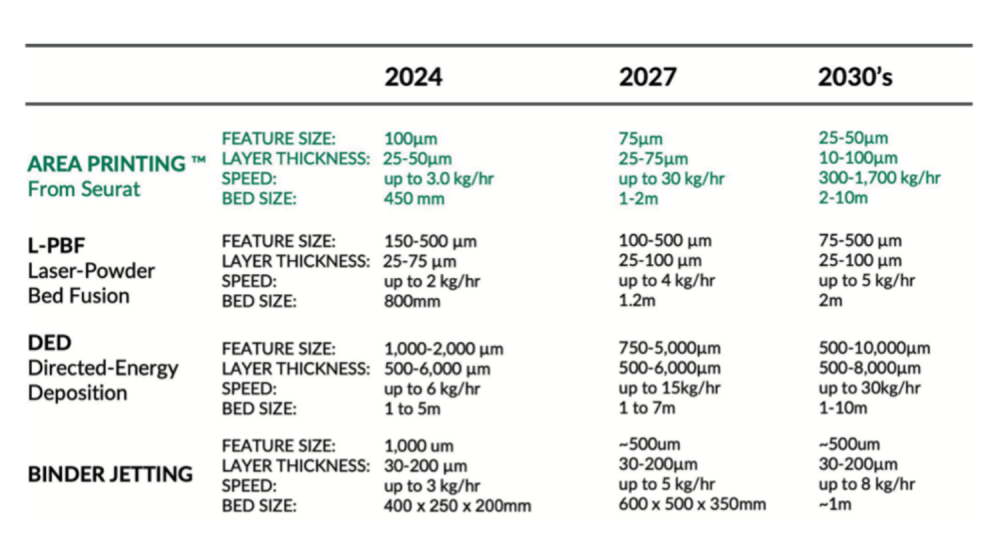
Рис. Сравнение ключевых характеристик и потенциала развития популярных АТ и технологий нового поколения (Seurat, Ampower)
Однако для их внедрения потребуется подготовить соответствующую инфраструктуру, развить инженерное мышление и провести длительные испытания. Только тогда современные лазерные и электронно-лучевые технологии, которые сегодня считаются максимально зрелыми, могут оказаться в категории «устаревших».
Но пока этого не произошло: российский рынок не создаёт принципиально новые решения, а идёт по проверенному пути, сформированному в те времена, когда границы были открыты для посещения международных выставок и общения с коллегами из науки и бизнеса. Проще говоря, сегодняшние технологии в России — это результат планомерного, а иногда и хаотичного развития с опорой на мировой опыт прошлых лет.
В таких странах, как США, ЕС и Китай, государственная поддержка IT, искусственного интеллекта и инноваций в производстве создала благоприятную среду для появления множества стартапов с перспективными решениями. Этот подход стимулирует конкуренцию и ускоряет внедрение передовых технологий.
В России ситуация отличается. Отечественные разработчики часто вынуждены наблюдать за успехами зарубежных коллег со стороны, порой с завистью, но не обсуждают это открыто. Их позиция объяснима: в условиях ограниченного рынка они сосредоточены на продвижении собственных решений, стараясь убедить промышленников в их идеальности и конкурентоспособности.
Вызовами для российских разработчиков является высокая конкуренция в базовых технологиях, а также ограниченное развитие новых технологий. Особенно остро эти вызовы проявляются в сфере 3D-печати, где российские компании активно конкурируют за внимание промышленников, стараясь позиционировать свое оборудование и программное обеспечение как лучшие на рынке. Это порождает многочисленные дискуссии внутри профессионального сообщества и усиливает необходимость в поддержке инноваций на государственном уровне.
Нельзя утверждать, что Минпромторг РФ полностью игнорирует необходимость поддержки отечественных компаний в сфере АТ. Такая помощь действительно существует, но она пока не носит массового и системного характера. При этом ключевыми барьерами для развития отрасли остаются бюрократическая нагрузка (отчетность и долгие процедуры согласования), и недостаток частных инвестиций (инвесторы в России неохотно вкладываются в АТ, предпочитая проекты с быстрым и гарантированным возвратом средств. Для них критично видеть ясный бизнес-план: серийный продукт, который 3D-принтеры смогут выпускать стабильно и в течение многих лет).
Готовы ли российские компании к таким вызовам и барьерам? Далеко не всегда. А к чему же они готовы? Судя по многим кейсам и комментариям в профильных группах в соцсетях, они часто сосредоточены на… тюнинге! Тюнинг автомобилей? Лишь частично.
Технологии цифрового АП за более чем 40-летнюю историю прошли путь от быстрого прототипирования до полноценного промышленного сектора, ориентированного на выпуск конечных изделий и оснастки. Однако об этом знают далеко не все промышленники. Большинству на глаза чаще попадаются проекты и детали, которые не имеют «взрослых» атрибутов: серийности, точности, повторяемости, эксплуатационной эффективности. Показать им такие атрибуты могут компании и эксперты, кто давно и успешно занимается продвижением промышленного АП.
Доступность технологий, особенно для работы с полимерами, породила целую армию мейкеров (DIY, сторонников движения «сделай сам»), а также школ, колледжей, университетов и студий дизайна, использующих 3D-печать. Компании-разработчики 3D-принтеров, ориентированные на массовый потребительский сегмент, где требования к промышленному качеству минимальны, в своей рекламе делают акцент на индивидуальные прототипы, игрушки, интерьерные элементы, ремонт или тюнинг.
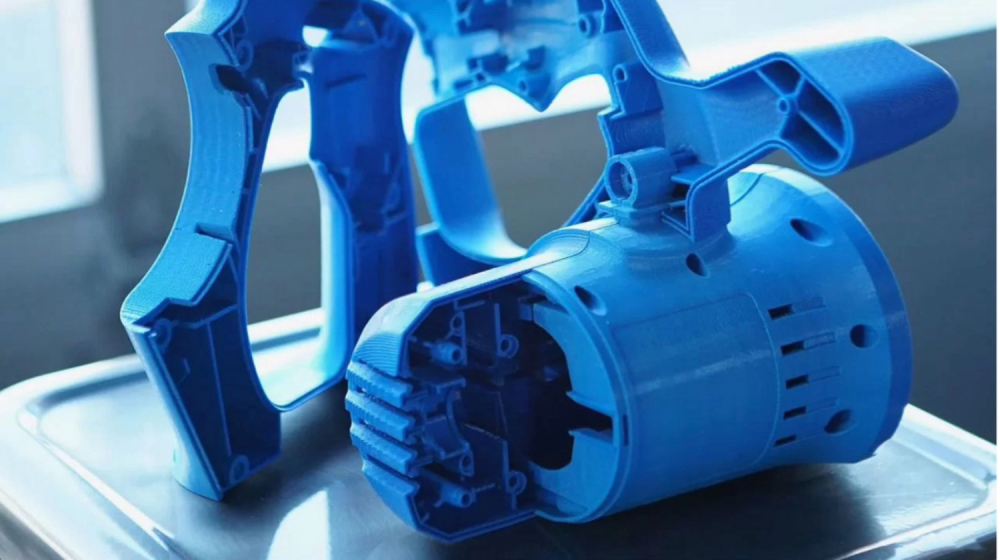
Рис. Корпус для электроинструмента
Очевидно, что такой простой и пассивный подход вдохновляет индивидуалистов, которые получают в своё распоряжение своеобразный «швейцарский нож», способный справиться с практически любой повседневной задачей. В результате рынок наполняется предложениями от небольших студий и 3D-ферм, которые могут выполнить обратный инжиниринг (используя штангенциркуль, линейку или 3D-сканер) и выполнить единичные или мелкосерийные заказы, в основном из полимеров и композитов.
Центрам аддитивного производства (ЦАП) и студиям с системами 3D-печати по металлам повезло чуть больше. Помимо дорогостоящих принтеров, они нередко располагают высокоточными 3D-сканерами, а иногда и координатно-измерительными машинами или томографами. Некоторые из них могут позволить себе лаборатории для тестирования материалов, механическую обработку с ЧПУ и термообработку. Такие возможности открывают доступ к более сложным задачам. Сегодня заказчики всё чаще обращаются с запросами на ремонт вышедших из строя деталей, которые сложно заказать из-за санкций. Также популярны заказы на прототипы или пилотные партии продукции, которая впоследствии будет изготавливаться традиционными методами (литье, штамповка, механическая обработка). Для целей испытаний, патентования или участия в отраслевых выставках бывает необходимо изготовить небольшое количество деталей, и сделать это быстро и без применения оснастки практически невозможно без АТ.
Отдельного внимания заслуживает использование топологической оптимизации или генеративного проектирования – это высший уровень мастерства для тех, кто понимает возможности АП. Здесь речь идёт о целенаправленной работе над созданием изделия с новыми потребительскими свойствами, соответствующими мировым стандартам.
Нельзя не отметить тот огромный вклад, который сделали и делают многочисленные производители и интеграторы аддитивного оборудования и решений для 3D-сканирования в России. Однако многие из них, будь то из-за недостатка опыта, знаний или из-за кажущейся простоты, сосредотачиваются на разрозненных проектах с намерением помочь каждому. Такие подходы, несмотря на многочисленные «успешные» истории, редко приносят ожидаемую инвесторами значительную прибыль. Большая часть времени уходит на ремесленную работу с каждым заказчиком, что не способствует масштабируемости. Промышленники, наблюдая за этим, начинают ошибочно считать, что АТ не подходят для серийного производства. Так незаметно проявляется пресловутый эффект Даннинга-Крюгера.
Кто мешает промышленным предприятиям глубже изучить потенциал АТ для производства? Формально – никто. Но готовы ли компании выделить на это ресурсы, а их руководители – углубиться в сложную техническую тему? В реальности многое зависит от уровня компетенции и подхода к управлению.
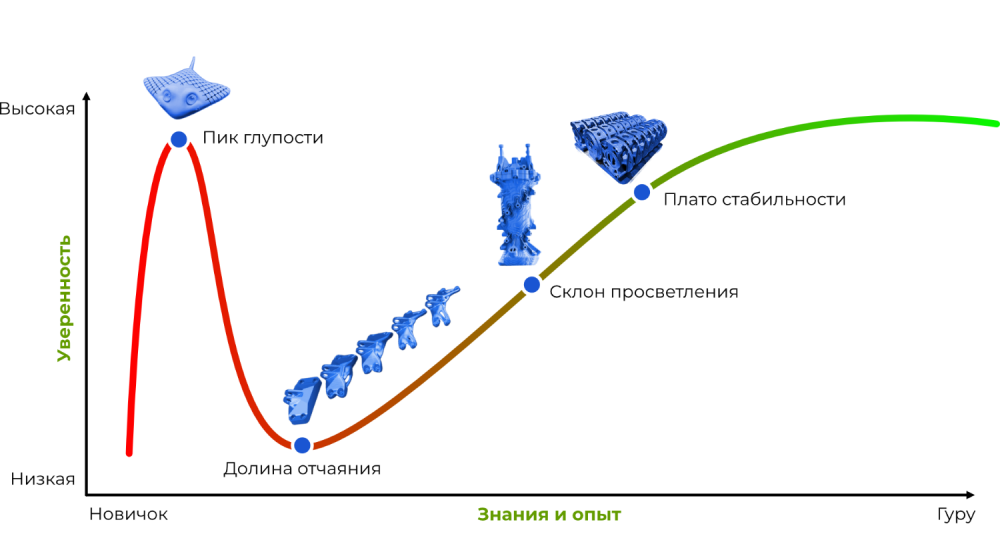
Рис. Диаграмма с эффектом Даннинга-Крюгера
Новички и небольшие мастерские заполняют новостной фон красивыми, но единичными кейсами, которые больше подходят для саморекламы. Они с энтузиазмом показывают: «Вот что мы можем, и у нас есть ещё масса идей!». В то же время опытные специалисты, погружённые в решение сложных задач, остаются в тени и не создают яркой информационной повестки.
В результате складывается впечатление, что ниша серийного АП в России остаётся незаслуженно обделённой вниманием и практически свободной.
Пришло время её занять!
Трубашевский Дмитрий, эксперт аддитивных технологий, генеральный директор ООО «Синтезиум»
Биленко Павел, директор по развитию ООО «Синтезиум»
Опубликовано в журнале Монокль.