На недавнем форуме в Великобритании – AMUK, Люк Фокс рассказал о том, как 3D-печать используется для совершенствования производства автомобилей класса люкс в Великобритании. Технический специалист по аддитивному производству британской автомобильной компании Jaguar Land Rover (далее JLR), Фокс рассказал о критической роли АП в рабочем процессе компании. Примечательно, что 3D-печать не используется для крупносерийного производства деталей конечного потребления. Вместо этого ее ценность заключается в удовлетворении растущего спроса на массовую кастомизацию, а также в ускорении производства функциональных прототипов для тестовых автомобилей. Последнее представляет собой “подавляющее большинство компонентов”, которые JLR производит внутри компании в своем Центре аддитивного производства (AMC). Фокс подчеркнул важность этих аддитивных возможностей, заявив, что без 3D-печати “мы не смогли бы проводить испытания так быстро”. Технический специалист также рассказал о том, как аддитивное производство решает одну из наиболее актуальных проблем, стоящих перед автомобильной промышленностью. Многие сроки экологической безопасности автомобилей быстро приближаются, и автопроизводители стараются минимизировать свой углеродный след и сделать свои автомобили соответствующими экологическому законодательству. По словам Фокса, 3D-печать сыграет важную роль в реализации обязательств JLR по достижению нулевого уровня выбросов в цепочке поставок к 2039 году.
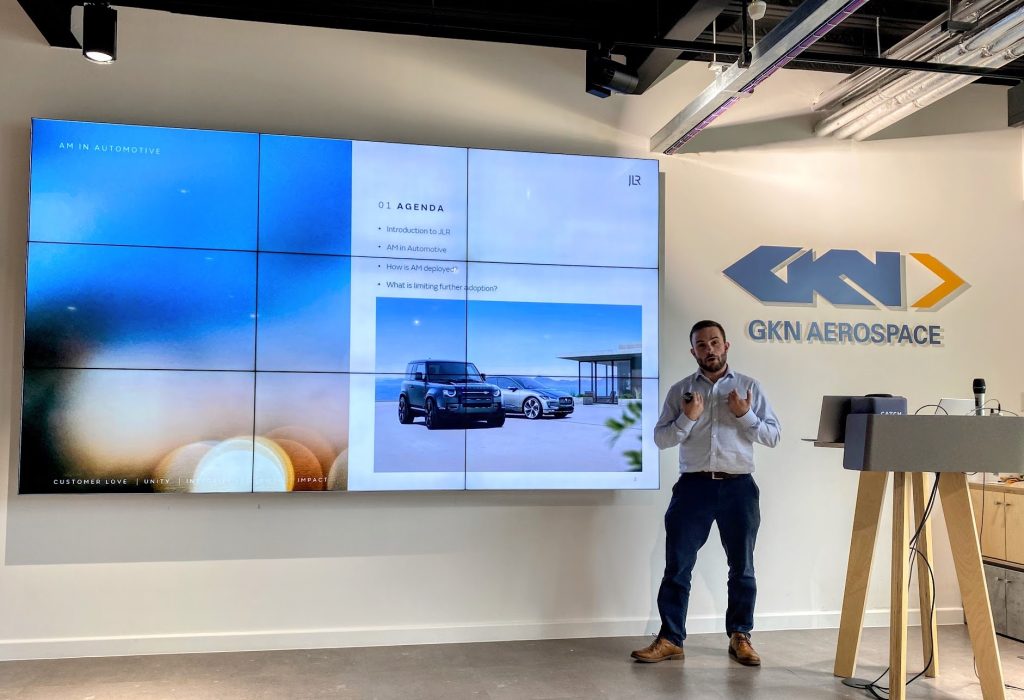
Люк Фокс выступает на Форуме членов AMUK. Фото 3D Printing Industry.
Additive Manufacturing UK (AMUK) – это торговая ассоциация компаний, работающих в британской экосистеме 3D-печати. Последний Форум членов ассоциации прошел в Глобальном технологическом центре производителя аэрокосмической техники GKN Aerospace, расположенном в Бритсоле. На мероприятии были представлены презентации, посвященные текущему состоянию аддитивного производства в Великобритании и его будущему направлению. У участников также была возможность пообщаться и насладиться эксклюзивной экскурсией по научно-исследовательскому и опытно-конструкторскому комплексу GKN.
В ходе своего выступления Фокс рассказал о глобальном охвате JLR, которая располагает тремя заводами по производству автомобилей в Великобритании и дополнительными заводами в Словакии, Бразилии, Китае и Индии. Компания, являющаяся стопроцентным дочерним предприятием Tata Motors, производит и продает автомобили марок Range Rover, Defender, Discovery и Jaguar. В 2018 году JLR обязалась производить миллион автомобилей в год. Однако Фокс пояснил, что с тех пор компания изменила свою стратегию, поставив во главу угла качество, а не количество, и в 2023 году будет выпускать около 400 000 автомобилей. Аддитивное производство играет ключевую роль в достижении этого качества.
В подразделении Additive Manufacturing Center (далее AMC) компании JLR, расположенном в центре Gaydon Advanced Product Creation Centre, установлено 20 промышленных 3D-принтеров, использующих шесть технологий аддитивного производства, общая площадь центра составляет подяка 4 000 000 кв.м.
Используются следующие технологии 3D-печати: MJF (HP Multi Jet Fusion), SLS (EOS), SLA (3D Systems), FDM и PolyJet.
На долю полимерного порошкового синтеза SLS приходится 87 % возможностей аддитивного производства компании. Полимеризация в ванне SLA составляет 8 % систем, а binder jetting и экструзия материалов – всего 3 % и 2 % соответственно.
“На данный момент мы занимаемся только полимерами, мы не делаем 3D-печать по металлу”, – добавил Фокс.
AMC действует как центр передового опыта в компании, выполняя различные функции – от создания ранних моделей до функциональных деталей.
“AMC создан как внутренний ресурс, – объясняет Фокс, – инженеры JLR из всех подразделений могут запрашивать 3D-печатные компоненты”.
Технология аддитивного производства также интегрирована в различные центры и отделы компании. Инженеры завода в Халевуде, одной из производственных площадок JLR, располагают примерно дюжиной промышленных 3D-принтеров FDM. Небольшие настольные системы FDM также распределены по другим производственным и инженерным площадкам. По словам Фокса, они используются для быстрого создания прототипов и тестирования, прежде чем поступают на AMC для изготовления более сложных деталей. Такой децентрализованный подход помогает поддерживать гибкость.
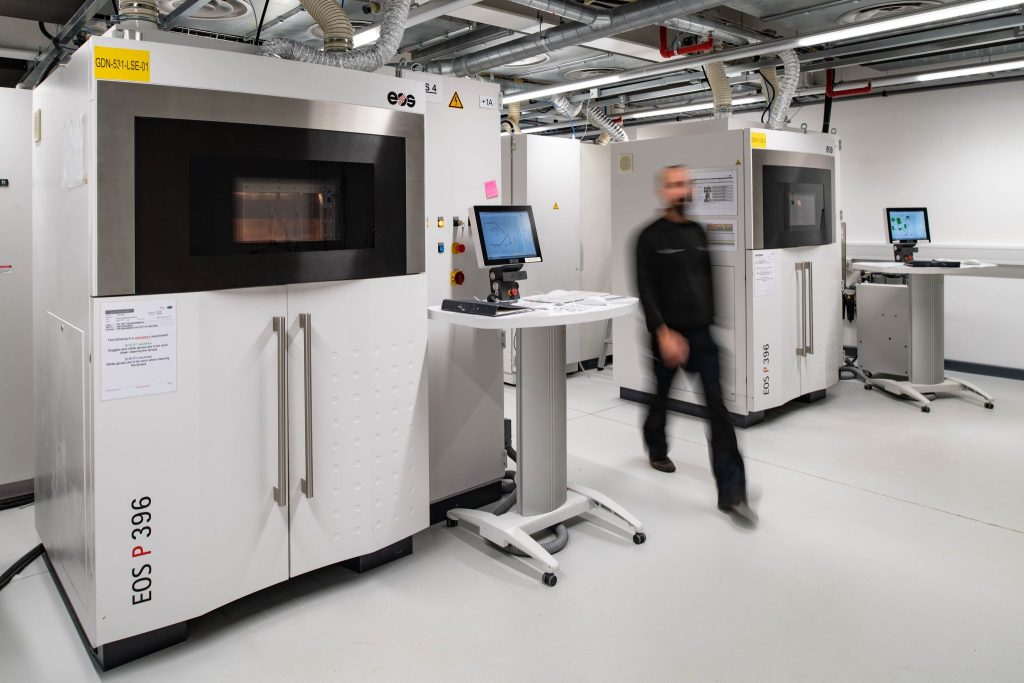
3D-принтеры EOS в Центре аддитивного производства JLR в Гэйдоне. Изображение предоставлено компанией JLR.
3D-печать улучшает разработку автомобилей
В прошлом JLR использовала аддитивное производство для изготовления конечных деталей автомобилей. Одним из ярких примеров является Jaguar XE SV Project 8 2019 года, в который вошло более десятка компонентов, изготовленных по технологии AMC. Среди них – крепление для переднего номерного знака, опоры для подголовников сидений и внешние аэродинамические элементы. Однако это была малосерийная продукция – всего 300 экземпляров Project 8. Более практичный вариант использования связан с устаревшими деталями. Фокс привел в пример повторяющуюся проблему с ручками сидений Land Rover Discovery 2 модели 1999 года – деталь, склонную к поломкам. Клиенты, владеющие этой моделью, теперь ожидают, что смогут заказать запасную часть в дилерском центре Land Rover. Однако компании, которая первоначально производила эти детали, больше не существует, а инструмент для литья под давлением был утерян. Решение JLR – 3D-печать деталей собственными силами, слегка изменяя геометрию для повышения прочности.
“Мы печатаем около 50 таких деталей в год”, – заявил Фокс, при этом клиенты часто даже не подозревают о том, что замена была напечатана в 3D.
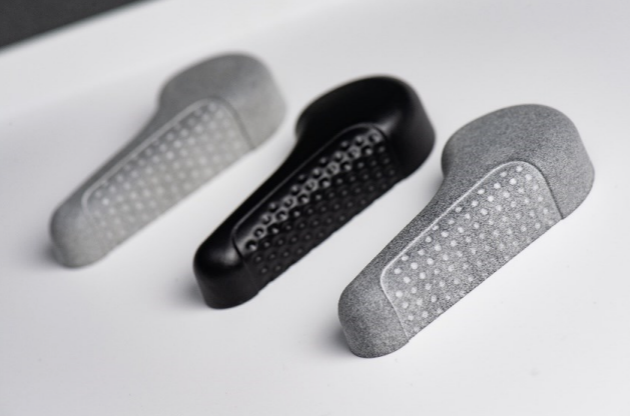
3D-печатные сменные ручки сидений Land Rover Discovery 2. Фото: Люк Фокс/JLR.
Массовая кастомизация – еще одно заметное применение АП в автомобилестроении. “Массовая кастомизация определенно не исчезнет, поэтому мы много занимаемся этим”, – заявил Фокс. Он отметил, что JLR активно работает над тем, как 3D-печать может позволить создавать более индивидуальные компоненты, такие как персонализированные крышки топливных баков и приборные панели. Однако “подавляющее большинство” усилий JLR в области аддитивного производства направлено на создание функциональных прототипов для тестовых автомобилей. Эти предсерийные автомобили часто обтягивают виниловым камуфляжем, чтобы скрыть их дизайн во время выставок и тестов на публике. Фокс заявил, что 3D-печать прототипов значительно ускоряет процесс тестирования, позволяя вносить изменения в дизайн и оценивать его гораздо быстрее, чем при использовании традиционных методов производства. Один из удивительных примеров постпроизводственного процесса связан с проблемой, с которой столкнулись владельцы внедорожника Land Rover Defender. “Когда они сажали свою собаку на заднее сиденье автомобиля, она царапала бампер”, – объяснил Фокс. Команда JLR, занимающаяся аддитивным производством, сделала 3D-сканирование лап собаки, проанализировала твердость когтей и напечатала 3D-копию лапы, которая была помещена на роботизированный манипулятор. Она неоднократно царапала бампер Defender “в течение очень долгого времени”, что привело к разработке защитной полосы, которую можно приобрести для минимизации повреждений.
Дорожная карта JLR по 3D-печати металлов
По словам Фокса, JLR будет работать над дальнейшим расширением использования аддитивного производства в будущем. Однако он отметил, что компания больше сосредоточена на расширении возможностей, чем на увеличении мощностей. Значительная часть этого развития связана с расширением возможностей 3D-печати металлов. Компания уже использовала внешнюю кооперацию для металлической 3D-печати для производства роскошных компонентов задней стойки для Range Rover SV 460. Эти детали изготавливаются поставщиком первого уровня, и в год производится около 40 таких деталей конечного использования.
“Хотя это и довольно малосерийное изделие, но уже сейчас оно используется в наших серийных автомобилях”, – добавил Фокс.
По мере расширения производства JLR работает над интеграцией металлической 3D-печати для более крупносерийного производства. Фокс рассказал о текущем проекте, в котором используется 3D-печать для поддержки производства “плюс-минус миллиона деталей”. Первоначально компания обратилась к лазерной порошковой плавке (SLM/PBF) для первоначального тестирования концепции. Затем команда решила изготовить “несколько сотен” металлических деталей для получения более строгих и точных результатов. Для этого они обратились к струйной печати на связующем, а в качестве окончательной серийной технологии производства выбрали порошковую металлургию MIM. Как сообщается, процесс струйной 3D-печати со связующим веществом позволил получить детали, близкие к желаемым механическим характеристикам. Фокс добавил, что такой подход позволяет проводить более обширные испытания и доработки без высоких затрат на традиционное производство металла, которое предполагает использование дорогостоящей оснастки.
Включение металлической 3D-печати в эту предпроизводственную фазу позволит JLR более эффективно дорабатывать дизайн перед запуском в серийное производство. Обсуждая более широкую стратегию компании в области АП, Фокс подчеркнул важность баланса между собственными возможностями и внешними партнерствами. Хотя JLR может создавать прототипы и тестировать детали собственными силами, для перехода к полномасштабному производству часто требуется привлечение специализированных поставщиков. “Мы не приспособлены к крупносерийному производству”, – признается Фокс. Его “вариант Златовласки” предполагает тесное сотрудничество с поставщиками в разработке и тестировании, а затем постепенную передачу ответственности по мере наращивания производства. Эта модель нашла отражение и в других автопроизводителях, включая Lamborghini. По словам Фокса, первоначально компания произвела 3D-печатную крышку топливного бака собственными силами, затем увеличила масштабы производства и в конечном итоге передала весь процесс на аутсорсинг, как только он был подтвержден. Такой подход позволил использовать преимущества возможностей аддитивного производства по индивидуальному заказу, передав при этом процесс массового производства третьей стороне.
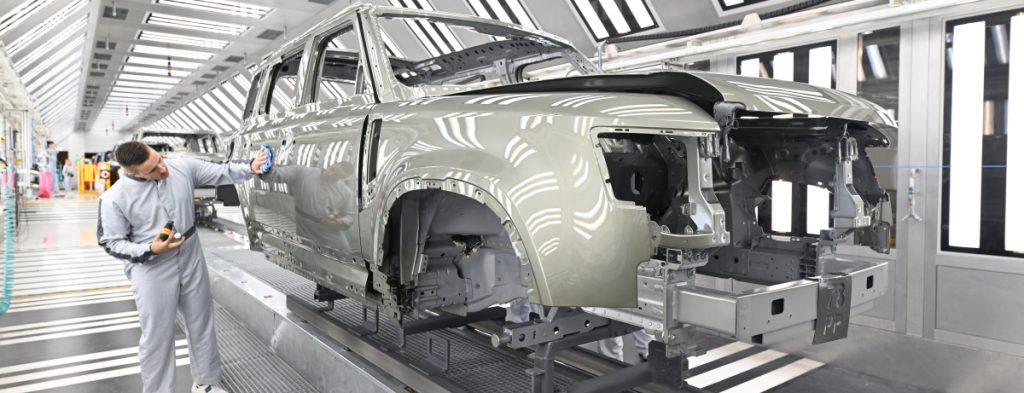
Производственная линия на заводе JLR в Нитре, Словакия. Фотография предоставлена компанией JLR.
3D-печать: будущее автомобильной экологичности?
Использование аддитивного производства растет в автомобильном секторе, что обусловлено требованиями экологического законодательства. Например, недавно было объявлено, что итальянский OEM-производитель 3D-принтеров Prima Additive сотрудничает с компанией Comau, занимающейся автоматизацией и робототехникой, для разработки 3D-печатаемого покрытия тормозных дисков. Этот процесс, как сообщается, может сократить выбросы загрязняющих веществ, связанные с деградацией тормозных дисков, на 80 %, что соответствует актуальным целям устойчивого развития. Стандарт Евро-7 Европейского союза (ЕС) требует сокращения выбросов частиц от тормозных дисков на 27 % к концу 2026 года. “Один из рычагов, за который мы можем потянуть, чтобы все больше и больше использовать АМ в автомобилестроении, – это то, что он более устойчив, чем другие традиционные производственные процессы”, – пояснил Фокс. Он назвал стратегию JLR по достижению нулевого уровня производства в 2039 году “очень, очень трудной задачей”, но подчеркнул, что компания стремится достичь этой цели, несмотря на увеличение расходов. “Мы готовы тратить больше, потому что наши клиенты готовы тратить больше на экологичный вариант”.
Примечательно, что бренд Jaguar, который в настоящее время выпускает только внедорожник F-Pace, стремится полностью отказаться от ископаемого топлива. Компания взяла на себя обязательство выпустить полностью электрический модельный ряд к следующему году. Как сообщается, все автомобили Jaguar будут построены на специальной чисто электрической модульной архитектуре. Ранее JLR объявила о планах инвестировать 3,5 млрд долларов США в год через компанию Tata для поддержки разработки новых электрических моделей и инфраструктуры. Бренд также работает над развитием других возобновляемых источников энергии наряду с электричеством.
Примечание редактора 3D Printing Industry
Опыт английских коллег подтверждает, что применение аддитивного производства позволяет быстрее выводить на рынок новые продукты (за счет параллельного этапа прототипирования и предсерии, и размещения на серийном поставщике), а также продолжать улучшать существующие изделия для постоянного повышения уровня качества.