В течение многих лет применение в автомобилестроении считалось несколько недосягаемой целью для индустрии аддитивного производства. Поставщики, исследователи и многие другие представители инвестиционного сообщества постоянно искали признаки успеха, которые свидетельствуют о “взрослении” индустрии аддитивных технологий. Это объясняется тем, что производство для автомобильной промышленности, по большому счету, приравнивается к массовому производству потребительских товаров, поэтому, если технология достаточно хороша для производства автомобильных деталей, из этого следует, что она будет достаточно хороша для широкого спектра потребительских рынков.
Однако многие не знают, что автомобильные компании были движущей силой многих основных разработок, лежащих в основе существующих сегодня технологий аддитивного производства, особенно тех, которые используются в производстве из полимеров. За некоторыми из первых успехов в использовании полимеров, естественно, последовал интерес к металлическому АП, и одной из компаний, которая, в частности, лидирует в этом отношении, является BMW.
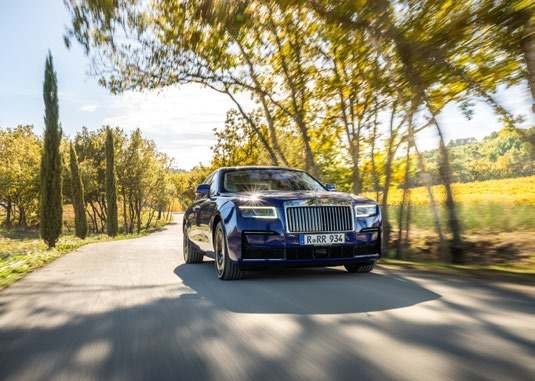
Рис. 1. Rolls-Royce Ghost оснащен многочисленными металлическими АП-элементами конструкции, которые производятся в кампусе компании BMW и ее внешними поставщиками. (Фото компании Rolls–Royce Motor Cars)
Компания BMW уже более трех десятилетий активно изучает возможности аддитивного производства, но в последние годы наблюдается всплеск активности по расширению использования металлических материалов. Кульминацией этого стало официальное открытие кампуса по аддитивному производству в Обершляйсхайме (Oberschleissheim), на окраине Мюнхена, в июне 2020 года. Строительство кампуса, строительство которого началось в апреле 2018 года, стало результатом первоначальных инвестиций в размере 15 миллионов евро и преследовало заявленную цель – помочь BMW Group укрепить свои позиции технологического лидера в области использования аддитивного производства в автомобильной промышленности.
«Однако у меня сложилось ошеломляющее впечатление,
что кампус является ступенькой к производству – демонстрационным заводом,
где апробируется и оптимизируется концепция
производства АП для автомобильной промышленности»
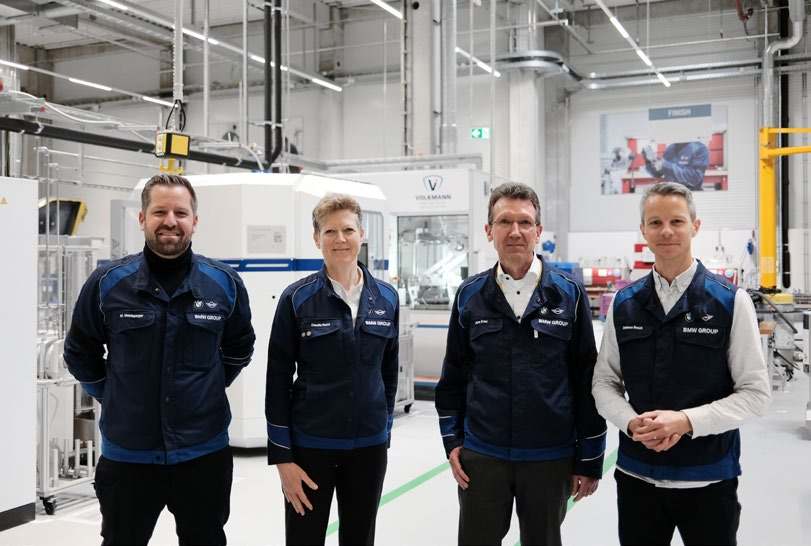
Рис. 2 Слева направо: Максимилиан Мейкслспергер, руководитель отдела аддитивного производства; Клаудия Ракль, руководитель проектов и квалификации в области аддитивного производства; Йенс Эртель, директор Кампуса BMW Group по аддитивному производству; и Стефанус Бош, руководитель отдела реконструкции и планирования аддитивного производства.
Когда людей просят представить кампус, большинство из них представляют себе открытые зеленые пространства с деревянными скамейками для обмена идеями и зданиями, предназначенное для образования и освоения технологий, с акцентом на обмен знаниями и партнерские отношения. Прибывая в кампус BMW АП, расположенный в большом современном промышленном комплексе, подтверждаешь эту идею. Здесь тщательно продуманы офисные помещения, конференц-залы и, конечно же, производственные помещения.
Атмосфера кампуса в определенной степени поддерживается благодаря идеально чистой окружающей среде, которая разделена на полимерную и металлическую зоны, в каждой из которых есть зоны для разработки процессов и материалов, экспериментов и совместной работы. Однако складывается впечатление, что кампус является ступенькой к производству – демонстрационным заводом, где апробируется и оптимизируется концепция производства АП для автомобильной промышленности.
Наш визит начался со знакомства с командой, в задачи которой входит создание такого впечатляющего объекта, во главе с Йенсом Эртелем, ветераном компании BMW и директором центра аддитивного производства BMW Group. Компанию Эртель поддерживает команда менеджеров, в состав которой входят Максимилиан Майксельспергер, руководитель производственного отдела аддитивного производства; Клаудия Ракль, руководитель проектов и квалификации в области аддитивного производства; и Стефанус Бош, руководитель отдела предварительной разработки и планирования аддитивного производства (рис. 2).
Аддитивное производство используется во всех четырех марках BMW – BMW, Mini, Rolls-Royce и BMW Motorrad – как для производства компонентов, так и для оптимизации производственных процессов в автомобилестроении. Несмотря на то, что металлические детали АП еще не используются ни в одном массовом автомобиле, очевидно, что они производились и продолжают производиться для автомобилей, выпуск которых исчисляется тысячами.
Некоторые из этих применений уже получили широкую огласку на протяжении многих лет, например, колеса с водяным насосом для гоночных автомобилей German Touring Car Masters (DTM) 2015 года выпуска, изготовленные методом лазерного напыления порошкового слоя (PBF-LB) (рис. 3), а также кронштейны для механизма открывания мягкого верха BMW i8 Roadster 2017 года выпуска, также изготовленные с использованием PBF-LB. Но не обманывайтесь, думая, что любое применение, разработанное в АП кампусе BMW, является “новинкой”, используемой для демонстрации возможностей металлического АП, – это далеко не так. Команда BMW подчеркивает, что любая деталь, которая запускается в производство, – это отнюдь не “PR-акция”, а скорее результат глубокого изучения экономической и технической целесообразности применения. BMW приступает к производству с использованием металлического АП только тогда, когда это дает убедительную экономическую выгоду.
Создание системы знаний об аддитивном производстве
Кампус поддерживает внедрение АП компанией BMW во всем мире и используется для формирования культуры инноваций, которая позволяет дизайнерам и инженерам понимать, как и когда использовать возможности технологии. Сотрудники приезжают в кампус, чтобы пройти обучение и получить навыки применения АП в своих подразделениях.
Для BMW, как опытного пользователя технологий АП, кампус представляет собой единый централизованный центр знаний по всем аспектам аддитивного производства. Компания сосредоточена на создании рабочей силы, понимающей возможности, которые АП предлагает бизнесу, и на роли обучения отдельных лиц на уровне продукта дизайну, процессам, свойствам материалов и экономике.
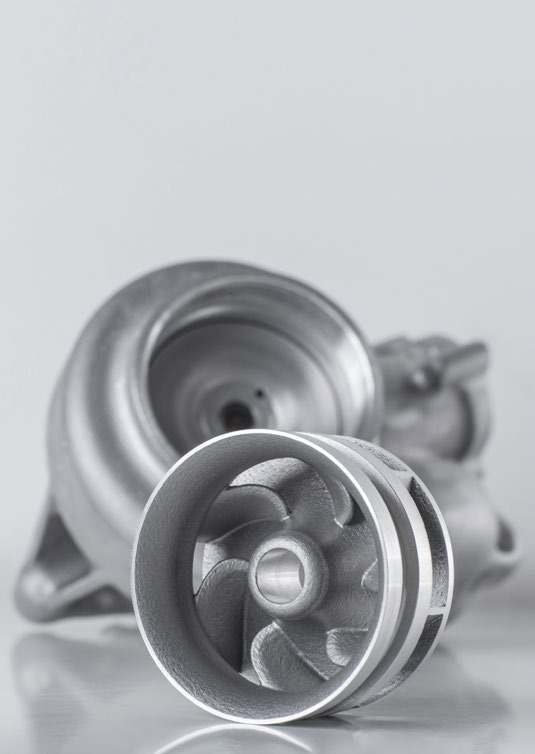
Рис. 3. Опубликованное еще в 2015 году, это цельное, легкое алюминиевое
колесо водяной помпы, изготовленное методом лазерного сплавления (PBF-LB),
использовалось в автомобилях BMW German Touring Car Masters (DTM), а также в автомобилях клиентов Z4 GT3 (Фото компании BMW).
Стремясь к глубокому пониманию АП и того, как технология отвечает потребностям бизнеса, BMW проявляет большую избирательность при внедрении технологий внутри концерна. Модель реализации проекта кампуса АП заключается не в том, чтобы “прилагать все усилия” для поиска потенциальных деталей для производства с помощью АП и последующего получения “низко висящих плодов”, а в сотрудничестве и разработке, экспериментировании с технологиями и материалами, подходящими для АП, разработке бизнес-обоснования и реализации его правильно с первого раза, когда принимается решение о запуске в производство.
«Компания сосредоточена на создании рабочей силы,
понимающей возможности, которые АП предлагает бизнесу,
и на роли обучения отдельных лиц на уровне продукта дизайну,
процессам, свойствам материалов и экономике.»
Возможность наблюдать за кажущимся непрерывным развитием технологий АП в отрыве от остальной производственной деятельности дает BMW возможность оценить реальную ценность АП для бизнеса и подумать о том, как это будет развиваться в дальнейшем.
Хотя, возможно, все еще верно, что металлическое АП ограничивается созданием прототипов и мелкосерийным производством, решения о том, когда тот или иной процесс АП подойдет для стандартных крупносерийных технологий, будут приниматься внутри кампуса, во многом так же, как принимаются решения об использовании литья, ковки или механической обработки и т.д.
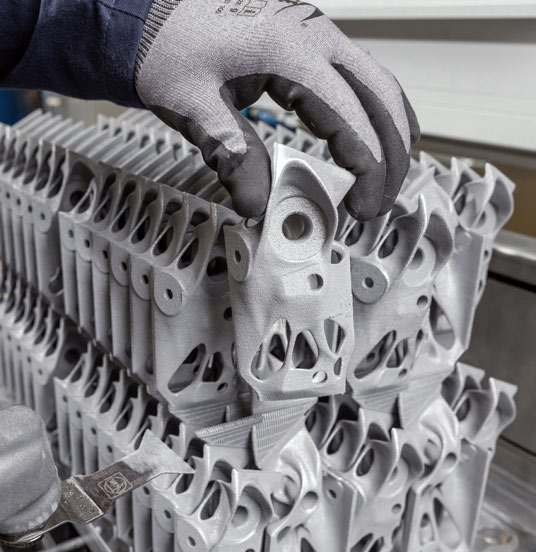
Рис. 4. Серийные детали, разделяемые в плотно упакованном пакете PBF-LB (Фото компании BMW)
«Хотя, возможно, все еще верно, что металлическое АП ограничивается созданием прототипов и мелкосерийным производством,
решения о том, когда тот или иной процесс АП подойдет для стандартных крупносерийных технологий, будут приниматься внутри кампуса.»
Ключевые технологии аддитивного производства из металла в BMW
Какие технологии BMW считает подходящими для автомобильной промышленности в настоящее время? Во время экскурсии по цехам кампуса, посвященному металлам, стало совершенно ясно, что основным направлением деятельности BMW является сплавление порошков с помощью лазерного луча (PBF-LB или SLM). Серийное производство осуществляется на станках Nikon SLM Solutions; также устанавливаются станки других компаний, в частности Trumpf и Additive Industries, но сложилось впечатление, что они не использовались для серийного производства. Из оборудования Nikon SLM Solutions в кампусе есть один SLM500-2 и два SLM500-4, оснащенные лазерами мощностью 700 Вт.
Несмотря на то, что в настоящее время в кампусе установлены исключительно европейские АП-машины, Эртель заявил, что будут рассмотрены машины из других регионов мира, но необходимо обеспечить ожидаемый уровень местного обслуживания и поддержки. “Мы открыты для покупки оборудования из-за рубежа, если сервисное обслуживание и запасные части организованы и гарантированы на месте”.
Когда дело доходит до серийного производства, мало кто станет возражать против того, что четыре лазера лучше, чем два, но выбор конфигурации станков PBF-LB в BMW является результатом многолетнего анализа. Мы были свидетелями того, как станки SLM500, оснащенные лазерами мощностью 700 Вт, использовались для серийного производства, причем эта конфигурация была основана на повышении производительности лазеров большей мощности. Команда разработчиков объяснила, что им удалось добиться более высокой скорости наращивания, используя слои порошка толщиной 100 мкм в сочетании с лазерами большей мощности, в отличие от стандартных слоев толщиной 50 мкм. Кроме того, сборка с использованием одного лазера на деталь гарантирует отсутствие дефектов при наложении узоров лазерного сканирования в любых областях наложения, что дает полную уверенность в том, что свойства не изменились в результате двойного воздействия.
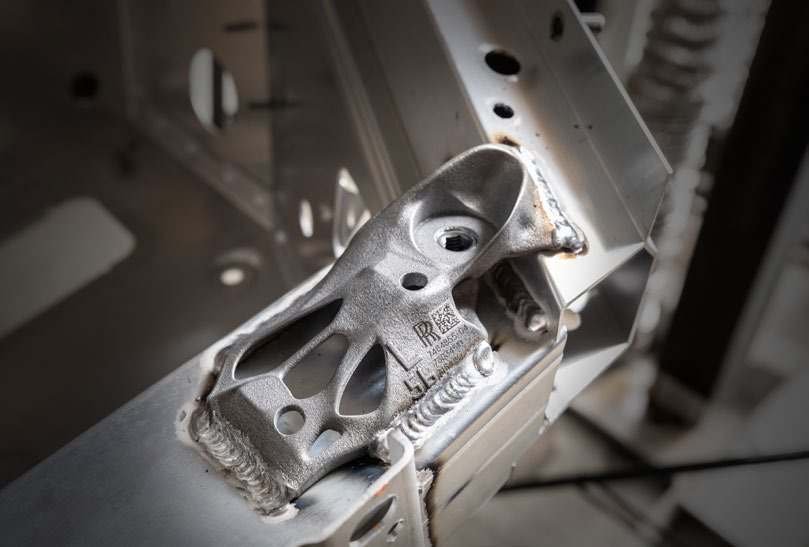
Рис. 5. Две машины для аддитивного производства SLM 500 HL PBF-LB от Nikon
SLM Solutions в кампусе BMW.
Довольно неожиданным был результат обработки поверхности, которого BMW добилась в этих сборках при использовании слоев толщиной 100 мкм. Было бы ошибочным решением увеличить скорость сборки только для того, чтобы ввести дополнительные требования к постобработке. Очевидно, что именно в этом заключается ценность работы, проведенной в кампусе. Это позволило команде точно определить требования к дизайну и последующей обработке.
Ожидается, что дальнейшее повышение скорости и производительности PBF-LB будет достигнуто благодаря разработкам в области технологий формирования луча. В рамках проекта, финансируемого Министерством экономики и борьбы с изменением климата Германии (Bundesministerium für Wirtschaft und Klimaschutz), BMW, Trumpf, Oerlikon Surface Solutions и Техническим университетом Дармштадта совместно работают над внедрением технологий формирования луча в производство. “Цель состоит в том, чтобы повысить производительность и снизить затраты на деталь (€/см3) с помощью процессов PBF-LB в автомобильной промышленности. Благодаря снижению стоимости деталей АП в будущем в автомобилях можно будет использовать больше оптимизированных по топологии легких компонентов, что позволит экономить энергию и выбросы CO2 в течение всего срока службы”, – заявил Максимилиан Биндер, специалист по технологиям АП в BMW Group.
Всё внимание на AlSi10Mg
Выбор материалов всегда будет одним из важнейших вопросов для любого производителя коммерческого транспорта. Как и во многих других отраслях, автомобильный сектор по-прежнему испытывает трудности с доступностью квалифицированных данных по сплавам-кандидатам. Поэтому одной из ключевых задач кампуса было получение необходимых данных.
Все детали PBF-LB, производимые на заводе, изготавливаются только из одного сплава – AlSi10Mg. Однако, учитывая, что этот сплав не может удовлетворить все потребности BMW, в настоящее время активно разрабатываются другие алюминиевые сплавы. Эртель заявил: “В прошлом были проведены разработки, позволяющие понять, какой материал подходит лучше всего, путем сравнения таких сплавов, как AlSi7Mg, AlSi9Cu3, AlSi12, на основе необходимых компонентов. Это привело к использованию AlSi10Mg. Сегодня, благодаря управлению технологическим процессом и термообработке этого базового сплава, мы можем изменять свойства материала, чтобы он вел себя так же, как и другие традиционные сплавы”.
Помимо этого – и за исключением мартенситностареющей стали (DIN 1.2709), которая в ограниченных масштабах используется для изготовления деталей и оснастки, – не было значительного спроса или интереса к другим распространенным автомобильным сплавам (например, сплавам Mg).
Автоматизация процесса
Серийное производство металлических деталей АП невозможно без необходимой постобработки для окончательной обработки деталей и управления движением материала. В кампусе BMW автоматизация постобработки получила значительное развитие. Проект “Индустриализация и цифровизация аддитивного производства” (IDAM), который осуществлялся с 2019 по 2022 год под руководством BMW в составе консорциума из двенадцати компаний, помог компании автоматизировать большую часть операций PBF-LB, повысив эффективность и, в свою очередь, значительно упростив производство дополнительных металлических деталей АП.
В частности, результатом проекта IDAM стала очень впечатляющая установка Volkmann в кампусе, которая соединяет машины PBF-LB с единой централизованной установкой для сбора и регенерации порошка (рис. 6). Трубопроводы, подводимые к каждой машине АП и отходящие от нее, проходят над главной магистралью цеха, демонстрируя, что перемещение металлических порошков на довольно значительные расстояния больше не является препятствием для будущей индустриализации производства металлических АП.
Аналогичным образом, последующая обработка готовой платформы построения начинается с удаления порошка. Для этого существует еще одна полуавтоматическая рабочая станция, которая способна принимать платформу построения любой конфигурации, потенциально, от любого типа станка PBF-LB.
В настоящее время разрабатывается полностью автоматизированная транспортная система (FTS), предназначенная для перемещения платформ построения АП между модулями на производственных линиях IDAM (рис. 7). Готовые изделия также могут быть переданы непосредственно на внутреннюю термообработку, размещенную в том же здании кампуса, а затем в другие отделочные цеха. В целом, это была очень впечатляющая установка, которая продемонстрировала полный комплексный производственный процесс.
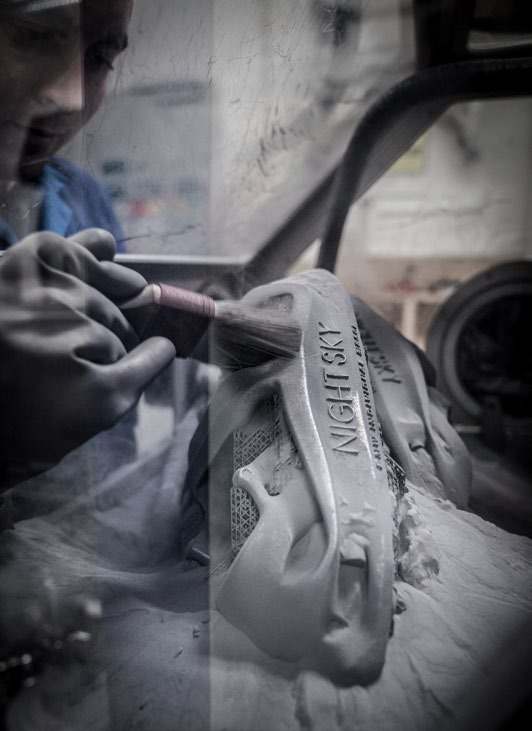
Рис. 6. Централизованная установка для сбора и восстановления порошка Volkmann, к которой подключены все производственные машины PBF-LB. Трубопроводы, ведущие к каждой машине АП и отходящие от нее, проходят над главной магистралью.
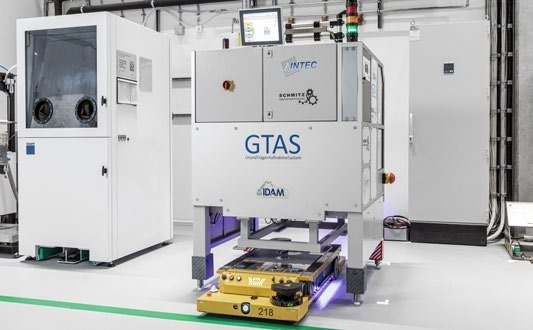
Рис. 7. Полностью автоматизированные транспортные системы без водителя (FTS), концепция которых была представлена в 2019 году, разрабатываются для перемещения мобильных камер сборки АП между модулями на производственных линиях IDАП (Фото компании BMW).
Успешная реализация проекта IDAM, который финансировался Федеральным министерством образования и научных исследований Германии (BMBF), позволила использовать опыт всех партнеров проекта. “С самого первого дня реализации проекта вы почувствовали командный дух партнеров”, – заявил Феликс Хеккель, лидер консорциума и руководитель проекта BMW Group. “Учиться друг у друга, совместно разрабатывать инновационные решения и наилучшим образом использовать индивидуальные сильные стороны каждого партнера – вот ключ к успешной индустриализации и цифровизации аддитивного производства”.
При обсуждении того, что BMW больше всего хотела бы видеть от производителей оборудования АП в будущем, немедленным ответом была совместимость. Наличие “универсальных” машинных интерфейсов позволяет автоматизировать технологические процессы на заводе-изготовителе. Четкий посыл заключался в том, что производителям оборудования АП следует сосредоточиться на своих сильных сторонах – на самом техпроцессе изготовления – и предоставить тем, кто обладает необходимым опытом, разрабатывать решения для подключения и автоматизации всех других этапов, необходимых на эффективном заводе АП. Кроме того, было заявлено, что будут приветствоваться улучшения в доступности, скорости построения и размере рабочей зоны.
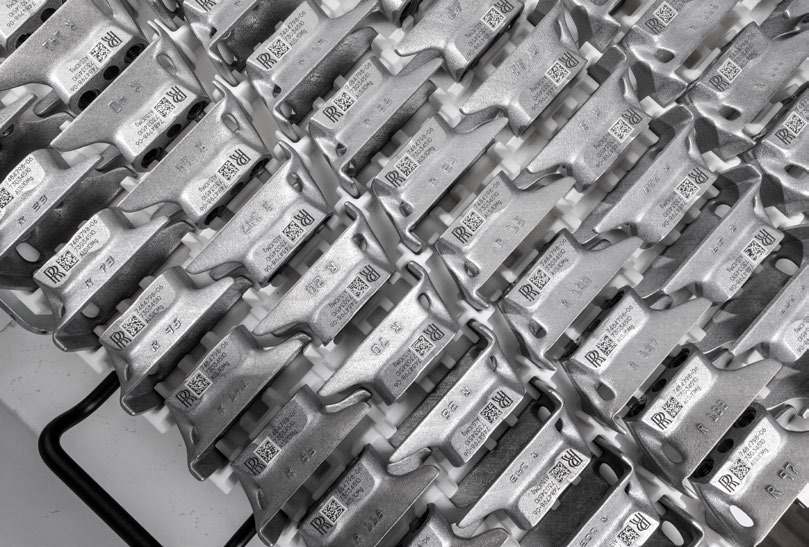
Рис. 8. Конструктивные элементы из сплава AlSi10Mg PBF-LB, разработанные кампусом АП, но произведенные на заводе BMW в Ландсхуте для Rolls-Royce Ghost (Фото компании BMW)
Последующая термообработка
Одной из важнейших целей в применении АП является достижение надежных и стабильных свойств материалов в произведённых деталях. В качестве важнейшего требования к качеству деталей BMW необходимо было найти новые способы термообработки, которые могли бы изменить свойства готовых деталей, чтобы они в точности соответствовали свойствам материалов традиционного производства, поскольку любые другие способы, отличающиеся по свойствам, привели бы к аннулированию существующих проектных данных.
В этом отношении именно проведенный командой анализ позволил им прийти к выводу, что гораздо проще добиться соответствия материалов известным свойствам и эксплуатационным характеристикам, чем вводить новые данные. Поэтому неудивительно, что предприятие оснащено собственной установкой для термообработки алюминиевых сплавов с печами для закалки и возрастного упрочнения.
Что касается квалификации процессов в АП, Эртель заявил: “Наш подход к общей квалификации процессов опубликован в стандарте ISO/ASTM DIS 52945, и критически важные для безопасности компоненты проходят дополнительное тестирование, но они ничем не отличаются от деталей, изготовленных обычными способами”.
Разработка запасных частей и рассмотрение цепочки поставок
Естественно, возникает вопрос, насколько коммерческая цепочка поставок далека от использования технологий металлического АП для производства деталей, способных удовлетворить потребности BMW. Команда ответила, что одна из причин их существования заключается в том, что цепочка поставок не готова к производству экономичных деталей, и даже если бы это было не так, в настоящее время на производстве недостаточно применений, которые могли бы это гарантировать.
Тот факт, что конструкция деталей и методы производства фиксируются при проведении омологации до начала производства, является препятствием для более широкого использования АП.
Для тех, кто не знаком с термином “омологация”, это процедура, которой должны следовать все автопроизводители, чтобы получить одобрение регулирующего органа на свою разработку. Это тщательный процесс, который гарантирует, что все продукты соответствуют требуемым стандартам и предписаниям по таким аспектам, как безопасность и воздействие на окружающую среду. Таким образом, после блокировки в серии ничего не может измениться до новой итерации дизайна. Это накладывает ограничения на использование АП для модификации любых существующих деталей, используемых в текущих моделях, поскольку они не могут просто начать производить детали с помощью АП и ожидать, что основные автомобильные бренды начнут использовать эти детали.
Этот процесс должен начинаться на ранней стадии жизненного цикла новой модели либо внутри автомобильной компании (например, в кампусе BMW в Обершляйсхайме), либо параллельно с конкретным предполагаемым внешним поставщиком. Поскольку это длительный процесс, он не обязательно зависит только от готовности внешних поставщиков.
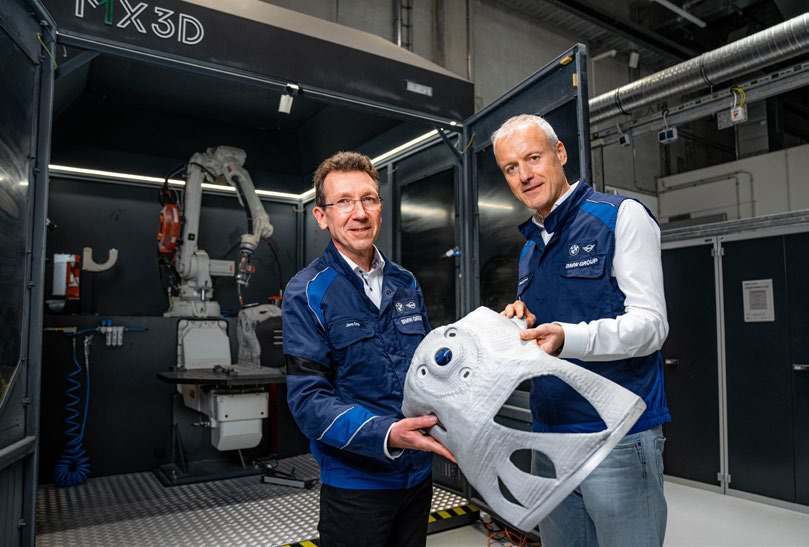
Рис. 9. Йенс Эртель (слева) и Кароль Вирсик, руководитель отдела исследований транспортных средств BMW Group, держат в руках большую деталь шасси, изготовленную с использованием технологии DED от MX3D (Фото компании BMW).
«Для тех, кто говорит, что технология еще не готова к массовому производству,
30 000 металлических деталей в год –
это не та цифра, от которой можно отмахнуться.
Конечно, в контексте автомобильной промышленности это небольшие цифры,
но прогресс можно только приветствовать.»
Однако было совершенно ясно дано понять, что этого также не произошло бы, если бы не было веских экономических обоснований для использования АП по сравнению с другими традиционными процессами.
Недавно BMW объявила, что в 2023 году на кампусе АП будет произведено около 300 000 деталей АП, а еще 100 000 деталей будут изготовлены на других заводах по всему миру. Эртель объяснил, что соотношение между пластиком и металлом составляет примерно 90:10. По мнению многих, кто проработал в АП-индустрии десять или более лет, производство десятков тысяч металлических АП-деталей в год всегда казалось “не за горами’. Для тех, кто говорит, что технология еще не готова к массовому производству, 30 000 или около того металлических деталей в год – это не та цифра, от которой можно отмахнуться. Конечно, в контексте автомобильной промышленности это небольшие цифры, но прогресс можно только приветствовать. И учитывая, что все эти запчасти АП производятся BMW только тогда, когда это имеет финансовую целесообразность, это следует воспринимать как необходимое доказательство того, что технология готова к массовому производству.
Чтобы управлять разработкой и применением АП и заказами для всей группы BMW, детали регистрируются в системе заказов AM.OS. Это индивидуальное решение объединяет систему управления жизненным циклом продукции BMW (PLM) с производственной сетью АП.
Потенциал технологии DED в автомобильной промышленности
Ограничения по размерам PBF-LB ограничивали разработку более крупных деталей АП в BMW. Несмотря на то, что на рынке появляются все более крупные машины PBF-LB, их цена и сложность в сочетании с высокой стоимостью порошка, необходимого для их наполнения, подталкивают к использованию в специализированных, дорогостоящих областях. Это стало одной из причин, по которой BMW решила изучить технологию электродуговой наплавки с направленной энергией (DED).
Станок DED голландской компании MX3D впечатляюще смотрится в цехе, отведенном для предварительной разработки (рис. 9). Очевидно, что BMW только приступила к оценке DED, но, тем не менее, была проделана впечатляющая работа. Неудивительно, что большая часть фактических исследований и разработок держится в строжайшем секрете; закрытость этой темы была очень заметна.
Используя технологию DED, BMW делает логичный шаг в направлении крупноформатного производства металлических деталей с АП. Этот процесс позволяет BMW изготавливать детали, которые легче и прочнее, чем аналогичные детали, отлитые под давлением, которые в настоящее время выпускаются серийно. Эти компоненты также могут производиться более экологично благодаря более низким энергозатратам и меньшему количеству отходов материалов.
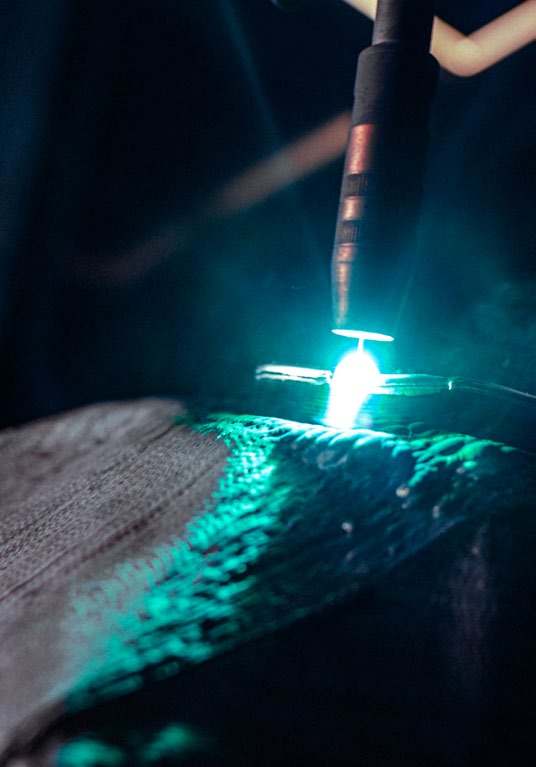
Рис. 10 Процесс DED на основе проволоки обеспечивает значительно более быструю и дешевое построение, чем PBF-LB, что делает его подходящим для крупных конструктивных элементов (Фото компании BMW)
«Используя технологию DED,
BMW делает логичный шаг в направлении крупноформатного
производства металлических деталей с АП.
Этот процесс позволяет BMW изготавливать детали,
которые легче и прочнее, чем аналогичные детали,
отлитые под давлением, которые в настоящее время выпускаются серийно.»
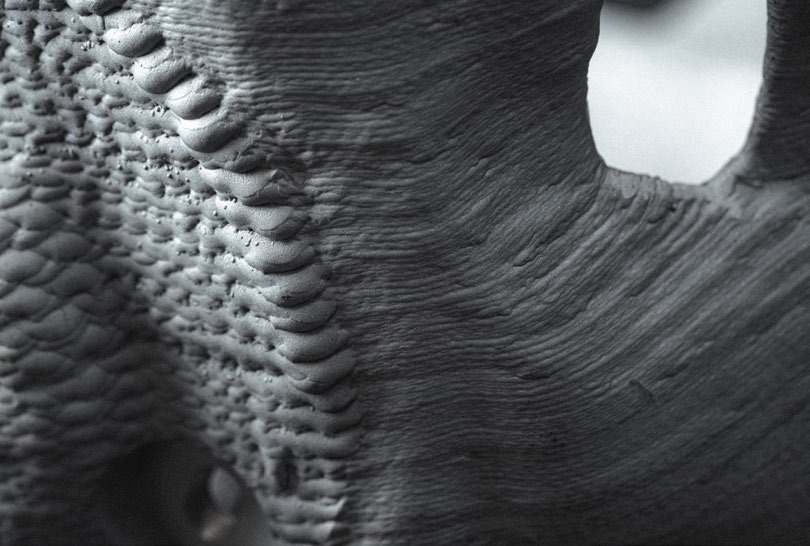
Рис. 11 Крупный план поверхности компонента, показанного на рис. 9. Компания BMW продемонстрировала, что компоненты DED могут использоваться при высоких нагрузках, в том числе циклических, без какой-либо последующей обработки поверхности (Фото компании BMW).
Типичная толщина стенок, которую позволяет изготовить DED, хорошо подходит для компонентов кузова, трансмиссии и шасси. В то время как BMW изучает процесс DED с 2015 года, машина MX3D была внедрена в 2021 году. “На этой ранней стадии уже ясно, что технология WAAM (Wire Arc Additive Manufacturing, альтернативное название wire/ arc DED) может привести к снижению выбросов в процессе производства. Меньший вес компонентов, выгодное соотношение используемых материалов и возможность использования возобновляемых источников энергии позволяют производить компоненты более эффективно”, – заявил Эртель.
Следующим этапом разработки на пути к серийному производству является тестирование компонентов в составе автомобиля; оно начнется в ближайшем будущем. Что касается примера детали шасси, показанного на рис. 9-11, то первоочередной задачей была минимальная постобработка: команда BMW полностью осознает важность использования режущего инструмента на детали АП с минимальными возможными затратами.
Более широкие сварочные швы в процессе DED означают, что поверхности деталей получаются рифлеными, а не гладкими. Несмотря на то, что критически важные участки, например, те, которые соединяются с другими компонентами, требуют механической обработки, BMW продемонстрировала, что компоненты DED могут использоваться при высоких нагрузках, в том числе циклических, без какой-либо последующей обработки поверхности. Оптимизированные параметры процесса изготовления имеют решающее значение для обеспечения долговечности со стадии производства, поэтому необходимо оптимально скоординировать процесс сварки и планирование траектории движения робота.
Чтобы максимально использовать потенциал процесса DED, критически важно комбинировать возможности производственного процесса и инновационную конструкцию новых компонентов. С этой целью BMW Group продолжает расширять использование генеративного дизайна, используя алгоритмы для проектирования оптимизированных компонентов на основе конкретных требований. Эти алгоритмы разрабатываются в тесном сотрудничестве с междисциплинарными командами.
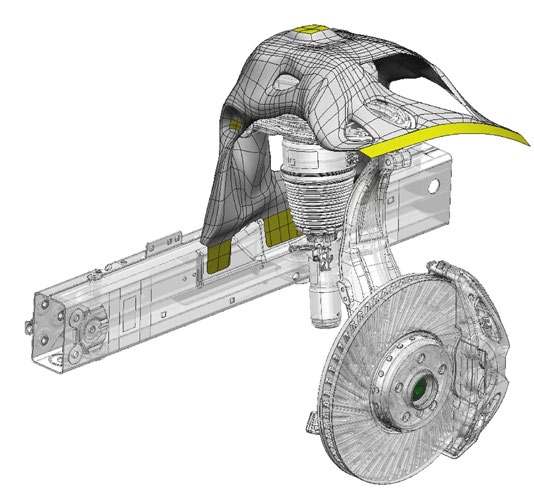
Рис. 12. Опора стойки подвески, изготовленная компанией BMW с использованием DED. Компания заявила, что использование методов генеративного проектирования позволяет ей в полной мере использовать свободу дизайна и, следовательно, потенциал технологии (Фото компании BMW).
Как и в случае с бионическими структурами, на первом этапе используется только тот объем материала, который действительно необходим для топологии компонента; во время тонкой настройки на втором этапе компонент укрепляется только там, где это необходимо. В конечном итоге это приводит к созданию более легких и жестких компонентов, а также к повышению эффективности и улучшению динамики автомобиля.
“Впечатляет то, как технология WAAM, основанная на исследованиях, превратилась в гибкий инструмент не только для тестирования компонентов, но и для серийного производства. Использование методов генеративного проектирования позволяет нам в полной мере использовать свободу дизайна и, следовательно, потенциал технологии. Всего несколько лет назад это было немыслимо”, – заявил Кароль Вирсик, руководитель отдела исследований транспортных средств BMW Group.
Заявленная цель BMW – использовать компоненты, изготовленные по технологии DED, в серийных автомобилях BMW Group. Учитывая более высокую скорость изготовления и значительно меньшую стоимость проволоки DED по сравнению с металлическими порошками для PBF-LB, будет интересно посмотреть, как DED развивается как потенциальная технология массового производства крупногабаритных компонентов автомобильных шасси, в отличие, например, от крупноформатных компонентов PBF-LB, используемых компаниями такие компании, как Czinger Vehicles в США.
Централизованное производство DED будет осуществляться в кампусе в Обершляйсхайме, хотя в будущем возможно производство в других местах и использование технологии поставщиками. Кроме того, с помощью этого процесса можно было бы даже производить отдельные компоненты по требованию непосредственно на сборочной линии. Во время нашего визита был сделан еще один интересный вывод, когда было сказано, что инженерным командам, не являющимся специалистами в АП, гораздо легче работать с DED, чем с PBF-LB, из-за широкого использования робототехники и сварки в более широких сферах деятельности BMW.
«Учитывая более высокую скорость изготовления
и значительно меньшую стоимость проволоки DED
по сравнению с металлическими порошками для PBF-LB,
будет интересно посмотреть, как DED развивается
в качестве потенциальной технологии
массового производства крупногабаритных компонентов
автомобильных шасси.»
Другие технологии аддитивного производства из металлов
Но что можно сказать о других технологиях металлического АП? Компания BMW быстро оценила потенциал технологии струйного нанесения связующего (BJT), что привело к ранним инвестициям в производство настольных систем из металла в 2017 году в рамках BMW iVentures. Однако в кампусе не осталось машин для струйного нанесения связующего, которые были сняты с производства из-за раннего развития технологии и ограниченного ассортимента материалов на тот момент. Эртель прокомментировал: “Интерес к этой технологии по-прежнему сохраняется, но решение использовать ее для производства деталей должно основываться на правильной экономической бизнес-модели и правильном выборе деталей. Возможно, те, кто занимается поставками в BMW, найдут больше возможностей для использования этой технологии, но до сих пор у нас этого не было”.
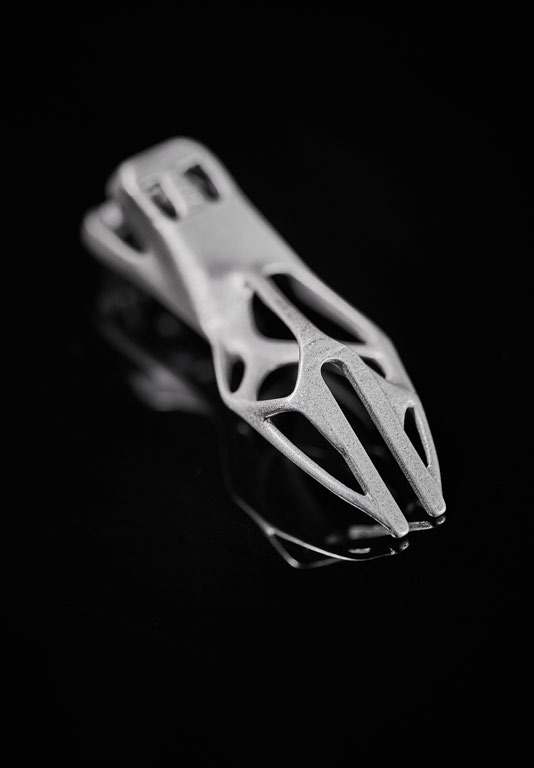
Рис. 13 Этот кронштейн, предназначенный для механизма откидной крыши родстера i8, был изготовлен в виде левой и правой пары в AlSi10Mg. Металлическая деталь легче и жестче, чем предлагаемая пластиковая деталь, с которой она конкурировала (Фото компании BMW).
Что касается других технологий обработки металлов, представленных на рынке, он добавил: “Поиск технологий является частью нашей предварительной разработки, но в настоящее время ни один другой процесс не считается достаточно зрелым, достаточно экономичным или даже достаточно близким с точки зрения логистики. Мы постоянно следим за появлением на рынке новых технологий АП и осуществляем стратегические инвестиции всякий раз, когда видим высокий потенциал”.
«Вы можете четко различить внутренние поверхности,
но BMW знает, что в данном случае это не имеет значения,
особенно для деталей, которые в основном незаметны.
Более того, в ходе работы в кампусе АП команда доказала,
что это не влияет на эффективность.»
Критические области внимания
Автомобильный сектор является строго регулируемым рынком, и внедрение технологий АП замедляется из-за отсутствия стандартов, автоматизации процессов, которые могут обеспечить квалификацию производства на основе данных, и других аспектов качества каждого типа процессов АП. Отсутствие нормативных стандартов для АП стало одной из причин создания кампуса АП, что позволило BMW провести множество собственных исследований и оценок возможных результатов в области качества АП.
В мире, который ожидает получения полностью готовых деталей с обработанными поверхностями, BMW задается вопросом, возможно ли изготавливать металлические детали АП без какой–либо или, по крайней мере, с минимальной постобработкой. Действительно ли качество поверхности так важно? Кронштейны, изготовленные для i8 Roadster (рис. 12), являются отличным примером успехов, достигнутых в этой области. Деталь легко снимается с платформы построения без применения электроэрозионной обработки или опиловки и проходит простую галтовку для выравнивания поверхности. Помимо лазерной маркировки, это все, что требовалось для изготовления готовых деталей. Невероятно, но эта деталь, изготовленная в виде пары левой и правой частей в AlSi10Mg, была легче, чем альтернативная пластиковая деталь, благодаря оптимизации топологии.
Конечно, если присмотреться к любой из этих деталей повнимательнее, можно увидеть много текстурированных (необработанных) поверхностей. Вы можете четко различить внутренние поверхности (на которых располагались поддержки), но BMW знает, что в данном случае это не имеет значения, особенно для деталей, которые в основном незаметны. Более того, за время работы в кампусе АП команда доказала, что это не влияет на эффективность.
Следующая область, которая, безусловно, вызывает озабоченность у BMW, – это себестоимость производства. Нет сомнений в том, что они считают, что еще многое предстоит сделать для того, чтобы сделать эти технологии жизнеспособными, но цены на оборудование и стоимость исходного сырья по-прежнему являются существенным препятствием для увеличения объемов производства, даже без ограничений, связанных с омологированным дизайном. Конструкции, сочетающие функциональность нескольких деталей или позволяющие избежать сложных операций сборки, уже стали реальностью. BMW применяет здесь осторожный подход и, очевидно, рассматривает детали для новых моделей только в тех случаях, когда инженеры-конструкторы могут объединить детали с помощью АП и выполнить основные критерии снижения общей стоимости.
Один из вопросов, который часто задают те, кто не знаком с АП из металла, особенно с PBF–LB, заключается в том, можно ли сваривать детали из АП. На самом деле, это любопытный вопрос, учитывая, что АП из металлического порошка на основе плавления – это не более чем непрерывная микросварка. Безусловно, в BMW также не возникало проблем со сваркой деталей АП (рис. 14). На производственной линии, по крайней мере, одной модели Rolls-Royce, используются дополнительно изготовленные алюминиевые пластины для крепления кузова автомобиля, которые изготавливаются с различной левой и правой геометрией и привариваются к кузову.
Сварка, безусловно, играет важную роль в производстве автомобилей, и команда BMW объяснила, почему технология металлического АП для быстрого прототипирования (RP) по-прежнему является ценным инструментом. Одним из интересных примеров является использование технологии металлического АП для изучения технологичности новой рамы мотоцикла. Здесь они даже воспроизвели искусственные сварные швы, которые станут частью каркаса, когда он будет изготовлен из профилей экструдированных стальных труб. Такого применения АП мы раньше не видели и, вероятно, даже представить себе не могли – и это несмотря на многолетний опыт поставки запчастей для сектора Формулы-1 и, в частности, для команд, проводящих испытания в аэродинамических трубах, где RP также по-прежнему широко распространен.

Рис. 14. Силовой кронштейн, используемый на Rolls-Royce Phantom, демонстрирующий свариваемость PBF-LB AlSi10Mg (Фото компании BMW)
Аддитивное производство песчаных форм и стержней
Несмотря на то, что сам по себе он не является металлической деталью, впечатляющим применением АП, которое мы увидели во время экскурсии, был очень большой роботизированный захват, отлитый из алюминия с использованием специально изготовленных песчаных стержней для отливок. Благодаря использованию АП и конструктивным преимуществам, которые оно дало, BMW снизила вес этого основного захватного устройства в три раза – всего до 50 кг. Интересно, что в то же время, когда мы увидели это устройство в металлическом исполнении, нам был представлен другой аналогичный по размеру захват АП из полимерно-композитного материала. Это важные достижения, которые часто остаются совершенно незамеченными и, конечно же, никогда не становятся целью для других компаний, когда они пытаются представить, какую пользу АП могла бы принести их собственному бизнесу. Представители BMW заявляют, что они считают усовершенствования оснастки и технологических процессов, которые могут быть достигнуты с помощью АП, не менее важными, чем попытки улучшить качество и/или удешевить детали с помощью АП, а возможно, даже более важными.
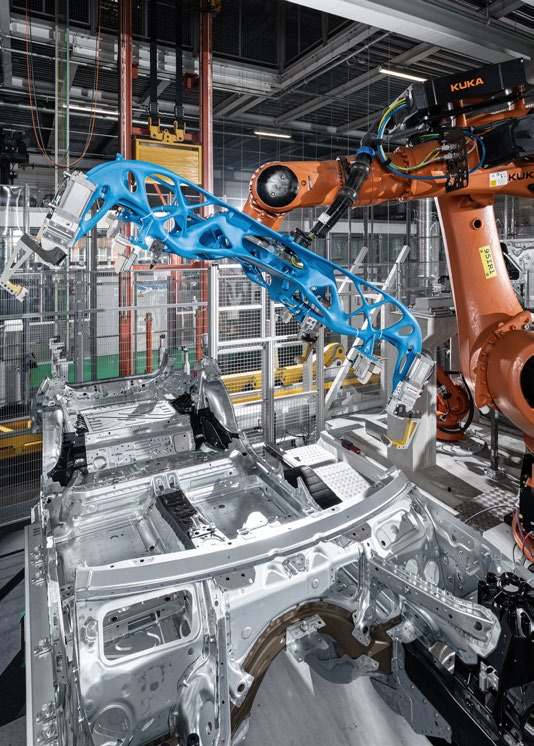
Рис. 15 Этот гигантский роботизированный захватный инструмент, отлитый из алюминия с использованием специальных песчаных стержней для отливок, был уменьшен в весе в три раза и составил всего 50 кг (Фото компании BMW).
Цепочка поставок
Ни один производитель автомобилей не может претендовать на то, чтобы быть на 100% вертикально интегрированной компанией, где все комплектующие для сборки производятся в четырех стенах. Следовательно, как и в большинстве промышленных стран, каждая компания полагается на цепочку поставок, которая обеспечивает ее всем необходимым для производства автомобилей.
Несмотря на то, что такие компании, как BMW, готовятся к изменениям, которые несет с собой АП, означает ли это, что их цепочка поставок готова отвечать будущим требованиям? Ответ на этот вопрос не однозначен. Как указывалось, ранее, из-за омологированного дизайна ни один производитель автомобилей не может просто так переключиться на поставщика запчастей АП для любых существующих компонентов для уже выпускаемого автомобиля. Это означает, что дизайн будущих моделей автомобилей, в которых будут использоваться запчасти АП, станет катализатором для цепочки поставок. По крайней мере, для этого у BMW есть стандартная практика для квалифицированных поставщиков; если бы им понадобилась услуга или запчасти АП по субподряду, то процесс ничем бы не отличался.
Что касается автомобильной промышленности в целом, то, если верно старое клише “прилив поднимает все суда”, то, возможно, расширение межотраслевого сотрудничества приведет к ускоренному внедрению АП в качестве технологии серийного производства. Это может означать более тесное взаимодействие с поставщиками верхнего уровня и другими автопроизводителями. Однако возникает проблема, если учесть, что этот сектор известен своей секретностью в отношении своих разработок, и BMW в этом отношении не является исключением. Однако команда сразу же отметила, что у них нет политики “закрытых дверей” в отношении сотрудничества. “В принципе, мы открыты для сотрудничества с производителями оборудования, органами стандартизации и другими промышленными партнерами, а также университетами”, – пояснил Эртель.
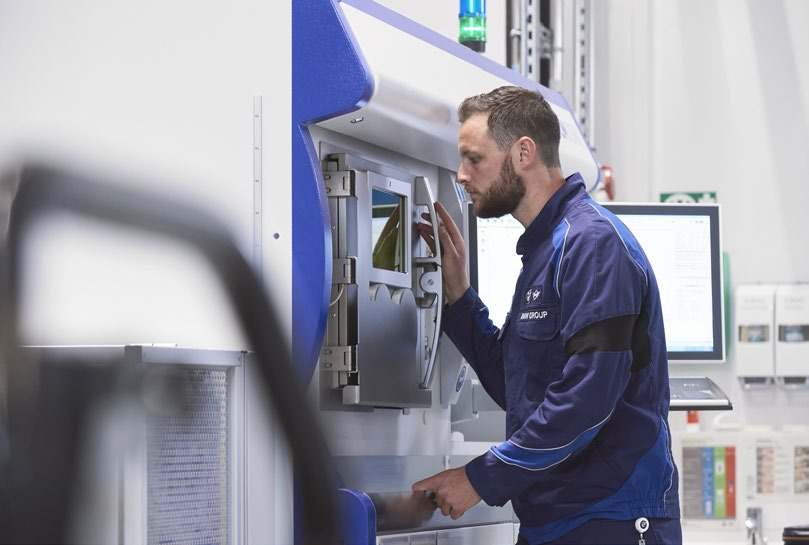
Рис. 16 Наблюдение за производством металлических деталей АП в кампусе BMW АП (Фото компании BMW)
Это еще раз подчеркивает важность понимания ограничений, связанных с возможностью планирования использования деталей АП только в новых моделях, и только там, где это имеет экономический смысл. Это позволяет реализовать долгосрочное видение, которое расширяется, хотя и не контролируется АП, а также означает, что традиционное производство будет использоваться еще очень долгое время.
Заглядывая в будущее, можно сказать, что в то время как более широкое сообщество АП с некоторой тревогой относится к более широкому применению этой технологии, приятно осознавать, что BMW считает, что роль металлического АП продолжает расти. Но предстоит еще многое сделать, особенно в том, что касается затрат. Эртель сказал: “Важно понимать, что аддитивное производство – это еще один производственный процесс в арсенале, дополняющий другие технологии, а не заменяющий их. Аддитивное производство всегда используется, когда есть преимущество с точки зрения времени, стоимости и качества. Дальнейшее развитие аддитивного производства как технологии для серийного производства зависит от различных факторов, и одним из наиболее важных факторов является снижение материальных и производственных затрат”.
Это, пожалуй, самый распространенный фактор для любой отрасли, желающей внедрить технологии АП и максимально эффективно использовать инвестиции: Как можно сделать это достаточно экономичным, чтобы вытеснить традиционное производство? Неудивительно, что основными факторами затрат являются оборудование и сырье. Как правило, в первом случае используется более долгосрочная амортизация активов, но это вызывает нервозную реакцию, поскольку мир привык к быстрым изменениям в технологиях.
«Несмотря на то, что такие компании, как BMW,
готовятся к изменениям, которые несет с собой АП,
означает ли это, что их цепочка поставок
готова отвечать будущим требованиям?
Ответ на этот вопрос не однозначен.»
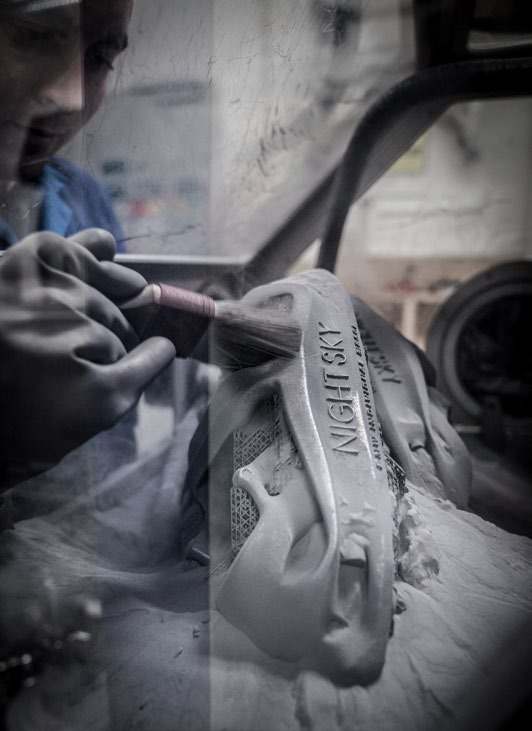
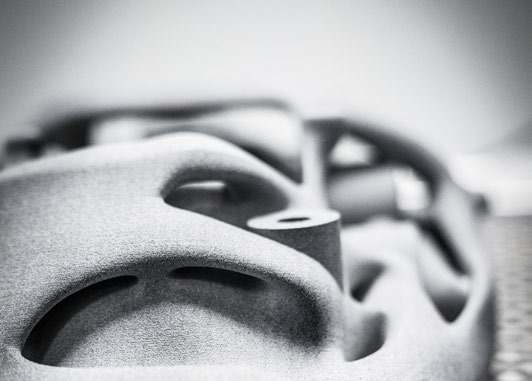
Рис. 17 Модель BMW Individual M850i NIGHT SKY edition, выпущенная в 2019 году, отличалась рядом деталей АП, в том числе большим тормозным суппортом. Облегченная конструкция позволила снизить вес до 30% по сравнению с обычной обработкой (Фото компании BMW).
Никто не знает, будет ли какая-либо машина по-прежнему считаться современной даже через два года, не говоря уже о десяти. Возможно, это объясняет, почему так мало других технологий АП представлено на выставке или активно эксплуатируется в кампусе. Зная, что лазерные станки мощностью 700 Вт подходят для изготовления алюминиевых деталей, BMW необходимо сначала добиться максимальной отдачи от этих станков в ограниченном ассортименте автомобилей четырех марок, использующих детали АП, прежде чем инвестировать в другие технологии.
Однако одной из областей, которая уже привела к значительному снижению затрат, является использование программного обеспечения, особенно при проектировании компонентов. Эртель подчеркнул подход BMW: “В случае серийных компонентов и деталей для других областей производственной системы геометрия всегда оптимизируется с точки зрения веса и технологичности. Это экономит вес / материалы и, следовательно, сокращает время и затраты на производство”. Таким образом, достижения в области проектирования при поддержке ПО и выбор применений, которые теперь включают сложные процедуры моделирования, позволили экономично использовать аддитивное производство на заводе BMW Additive Manufacturing Campus.
Команда специалистов по дизайну и инженеров сравнивает различные программные решения и использует их для разработки компонентов. Программное обеспечение явно изменило правила игры, и было заявлено: “Программное обеспечение больше не является ограничивающим фактором; на самом деле, чем лучше становится программное обеспечение, тем быстрее и качественнее могут быть оптимизированы компоненты”.
Заключения
BMW Additive Manufacturing Campus, несомненно, стал удачной инвестицией для компании, поскольку здесь сосредоточена самая большая концентрация оборудования и опыта в области АП. Несмотря на это, BMW располагает восемью филиалами по всему миру, в том числе в Мексике и США, где работает более 200 станков, работающих в области АП из полимеров и металлов.
Можем ли мы увидеть, что подобные кампусы появятся на какой-либо из этих территорий? Для этого потребуется особое стечение обстоятельств, и Эртель быстро объяснил, что это будет в значительной степени зависеть от наличия доступа к местной технологии АП. В конечном счете, расширение этого кампуса или любого другого объекта зависит от растущих потребностей остальной части группы. Эртель заявил: “Мы наблюдаем непрерывный и ежегодный рост применения аддитивного производства и производства деталей АП, включая металлические детали. Этот рост является результатом нескольких факторов, которые стимулируют использование аддитивного производства”.
При изучении этих факторов было отмечено, что аддитивное производство становится все более доступным и становится частью деятельности по разработке продуктов. Знания о технологии также растут, а возможности процессов АП постоянно оптимизируются, гарантируя соответствие требованиям испытаний при функциональной валидации. В совокупности эти факторы увеличат спрос на аддитивное производство и производство компонентов АП.
Польза аддитивного производства в автомобильном секторе ежедневно подтверждается в кампусе BMW АП, а также на заводе BMW в Ландсхуте. Несмотря на то, что уровень производства по-прежнему низок по сравнению с основными линиями по производству дорожных автомобилей, количество выпускаемых деталей АП исчисляется тысячами и десятками тысяч в год, экономическая целесообразность изготовления деталей для нескольких моделей более высокого класса привела к значительному увеличению производственных мощностей. Безусловно, из года в год производится всё больше АП деталей, как в автомобильной промышленности, так и в остальных отраслях, и это следует рассматривать как всеобщий положительный момент.
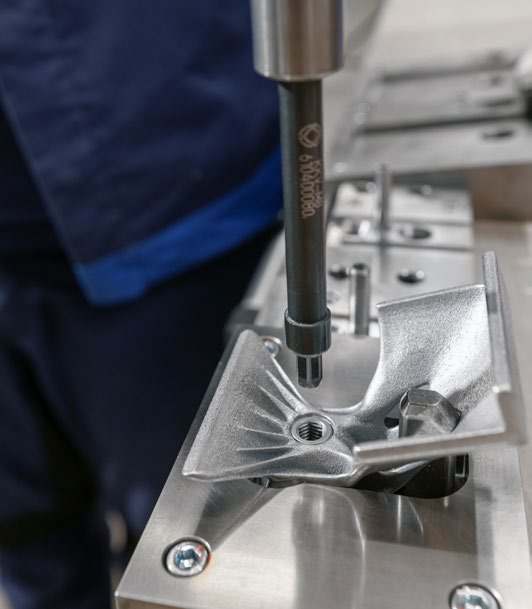
Рис. 18 Операции предварительной сборки компонента шасси PBF-LB (Фото компании BMW)
“Эффективность аддитивного производства в автомобильном секторе
ежедневно подтверждается в кампусе BMW…
экономическое обоснование производства деталей АП для нескольких высококлассных моделей
привело к значительному увеличению объема выпуска”.
Источник: Metal Additive Manufacturing Summer 2024