Перенеситесь мыслями на 20 лет назад и представьте список всех компаний, способных производить детали для аэрокосмической отрасли с использованием аддитивного производства (далее АП). Этот список был бы совсем не длинным. Однако в настоящее время на каждом континенте есть поставщики и целые программы, в которых аддитивное производство лежит в основе инноваций и разработок, а также отвечает за поддержание в рабочем состоянии стареющего флота. Несмотря на то, что на самом деле аддитивное производство из металлов развивается уже довольно давно, только за последние два десятилетия оно стало прорывной технологией. Эта разработка изменила возможности аэрокосмического сектора в производстве легких, сложных и высокопроизводительных деталей способами, которые ранее считались невозможными.
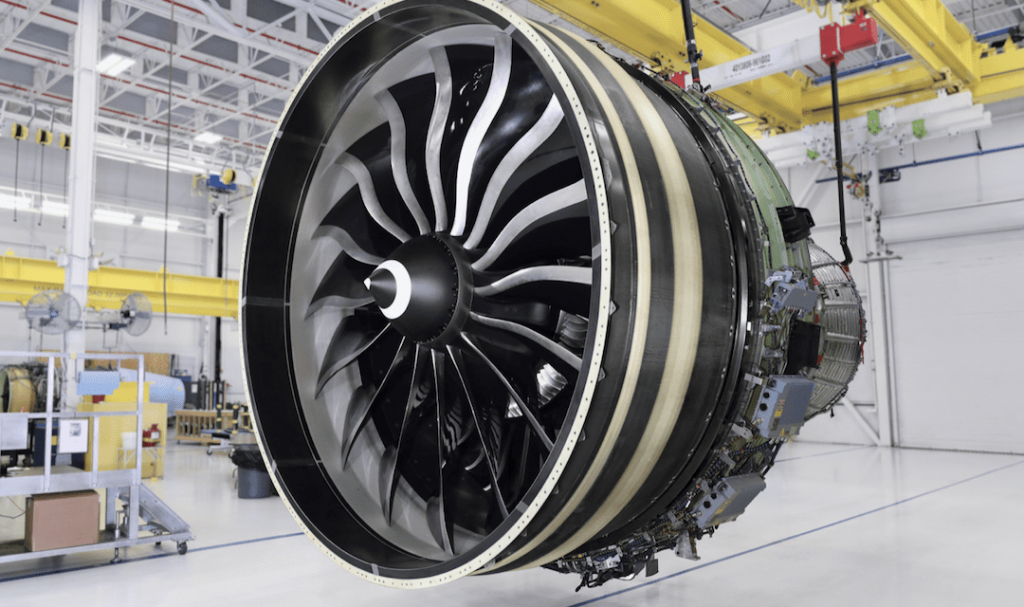
Рис. 1. Турбовентиляторный двигатель GE9X, содержащий более 300 деталей, изготовленных методом аддитивного нанесения металла, является наглядной демонстрацией возможностей АП. Двигатель был выбран компанией Boeing для своего авиалайнера 777X (фото компании GE Aerospace)
Возможность создавать сложные геометрические формы с внутренними элементами, необходимыми для охлаждения, и снижать вес за счет новых оптимизированных конструкций позволила повысить эффективность и эксплуатационные характеристики во многих областях авиационной и спутниковой техники. В настоящее время это касается как компонентов двигателей, так и конструктивных узлов, в критически важных для безопасности применениях. За последние 3-5 лет в отрасли значительно увеличилось число случаев использования деталей АП, предназначенных для замены деталей традиционного производства.
После действительно стремительного внедрения технологий АП, отрасль начинает сообщать о снижении затрат, сокращении сроков выполнения заказов, а в новую эру цифрового производства – о значительных улучшениях в гибких методах проектирования и разработки, основанных на моделировании и генерирующих алгоритмах. Благодаря такому использованию металлического АП авиационный сектор ожидает снижения выбросов CO2 как в производственных процессах, так и при конечном использовании изделий за счет снижения расхода топлива, также просматриваются привлекательные пути повышения экологичности. Топливную форсунку LEAP от GE Aerospace (рис. 2), которую мы рассмотрим здесь более подробно, можно рассматривать как первое крупномасштабное применение, подтверждающее истинность этих утверждений.
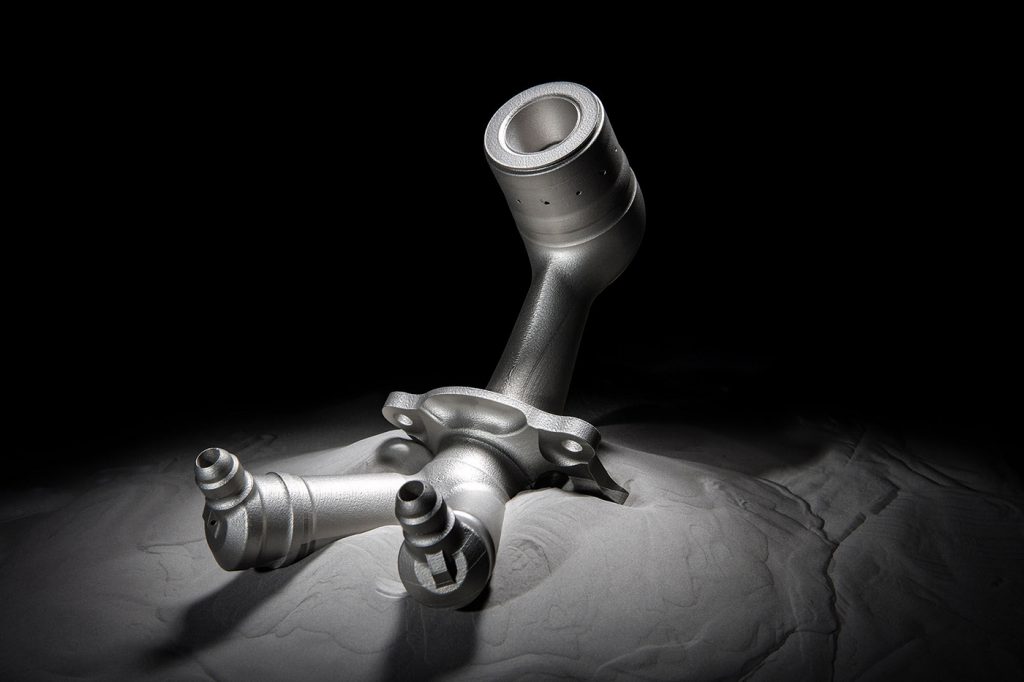
Рис. 2. Топливная форсунка LEAP от GE Aerospace, изготовленная для двигателей CFM International LEAP 1A и 1B. В каждом двигателе используется 18 или 19 топливных форсунок, изготовленных с использованием АП, в зависимости от конкретной модели двигателя. Двигатели используются на авиалайнерах Airbus A 220, A320neo, A321neo, Boeing 737 MAX и COMAC C919.
В 2021 году сообщалось, что наработка деталей превысила 10 миллионов летных часов и было изготовлено более 100 000 таких форсунок (фото компании GE Aerospace).
Все это произошло не в одночасье, и неуклонное внедрение в аэрокосмической отрасли “прорывных” технологий, таких как наплавка в порошковом слое (PBF), направленное энергетическое напыление (DED) и струйное нанесение связующего (BJT), проложило путь к беспрецедентным инновациям в проектировании деталей и разработке сплавов. Мир уже стал свидетелем первых пробных шагов основных производителей оборудования и поставщиков первого уровня. В этой статье будет рассказано о замечательных успехах, достигнутых с помощью этих технологий, выделив ключевые примеры, такие как лопатки турбин в двигателях и сложные устройства связи в спутниках. Немалый успех, учитывая глубокую неуверенность, существующую в отрасли, и защиту, подобную броне, которая окружает любое новое использование АП. Это само по себе вызывает недоумение даже у многих, кто работает в отрасли или является частью цепочки создания стоимости АП.
Мы не будем подробно останавливаться на объяснениях каждого из упомянутых процессов АП, поскольку в других источниках имеется обилие информации. Аналогичным образом, несмотря на то, что в настоящее время для целей АП в аэрокосмической отрасли разработано много новых сплавов, здесь недостаточно места, чтобы подробно рассказать о них. На самом деле, в открытом доступе имеется скудная информация, подтверждающая это. Вместо этого, способность металличесого АП поставлять детали массового производства, пригодные для полетов, рассматривается в обзоре тех деталей, которые уже одобрены и используются сегодня. Мы также планируем ограничить сферу нашей деятельности применением в авиации, поскольку на страницах журнала Metal AM регулярно публикуется информация о быстром росте применения АП в космосе.
Лазерное и электронно-лучевое синтезирование в порошковом слое: технологии, которые привели к революции.
Лазерное сплавление в порошковом слое (PBF-LB) и электронно-лучевое сплавление в порошковом слое (PBF-EB) являются доминирующими технологиями обработки металлов давлением, используемыми в аэрокосмической отрасли. Этот процесс относительно прост и позволяет быстро сканировать 2D-изображение лазерным или электронным лучом, чтобы выборочно расплавлять металлический порошок по одному слою за раз согласно 3D-модели.
Детали, изготовленные таким образом, практисески полностью плотные и в большинстве случаев подвергаются лишь ЧПУ-обработке и финишной обработке поверхности, после чего проходят самый строгий контроль качества. Таким образом, именно процессы PBF привели к величайшей революции в аэрокосмическом производстве за последние 20 лет. Эта группа технологий, для которой количество поставщиков станков по всему миру постоянно растет, действительно позволяет изготавливать более сложную геометрию и облегченные конструкции, одновременно повышая производительность компонентов – и все это при более низких общих производственных затратах. Главным достижением стала возможность отказаться от сложных методов сборки и соединения, объединив несколько деталей в единую конструкцию.
Ранний успех Northrop Grumman
Прежде чем подробно рассматривать более поздние примеры летающих или планируемых к лету деталей, стоит отметить, что самые ранние детали созданные с помощью PBF прошли квалификацию и были запущены в эксплуатацию. Эта честь, по-видимому, принадлежит компании Northrop Grumman, известной своей работой по решению сложнейших задач в аэрокосмической и оборонной отраслях с использованием передовых технологий, которые в настоящее время регулярно включают в себя аддитивное производство. Тайелор Маккей, главный инженер по системам аддитивного производства, заявил:
“Являясь пионерами в области передовых производственных возможностей, мы обладаем более чем двадцатилетним опытом в области аддитивного производства металлических изделий. Northrop Grumman воспользовалась многими преимуществами АП, такими как повышенная гибкость конструкции, консолидация деталей, повышение производительности, и смогла снизить затраты до 70%, а время выполнения заказа – до 90%”.
Довольно сложно найти много других примеров, относящихся к периоду до 2010 года, и компания Northrop Grumman сообщила, что в 1999 году она провела первую проверку на пригодность к полетам с использованием лазерно-порошковой технологии, а затем в 2007 году установила свой первый пригодный к полетам компонент PBF-EB из Ti-6Al-4V; система подогрева воздуха смеситель, используемый в X-47B – боевом авиационном беспилотнике ВМС США (рис. 3).
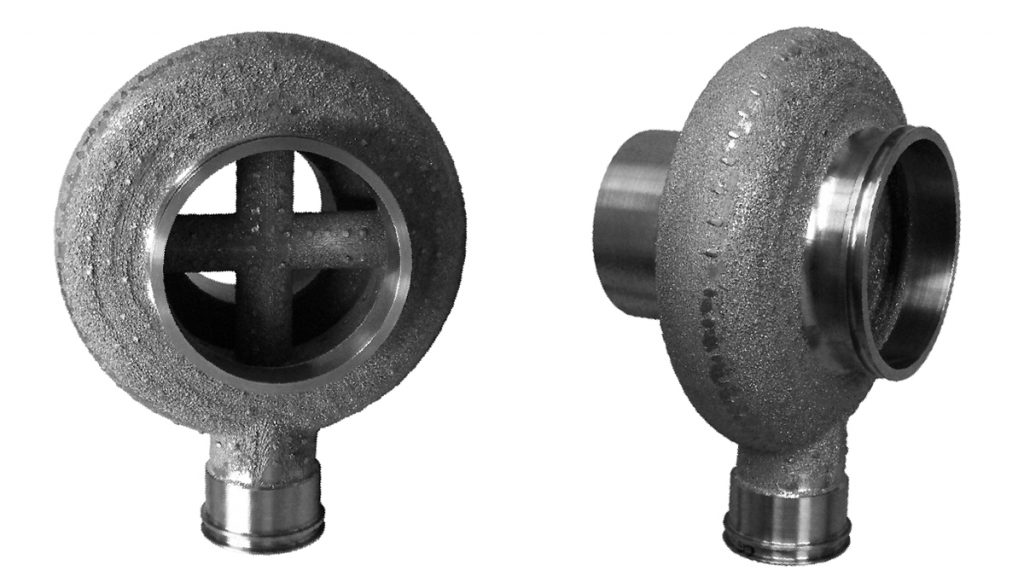
Маккей объяснил, как компания Northrop Grumman создала то, что считается первым авиационным компонентом из титана PBF, который был использован в реальных полетах, когда она поставила четыре детали для БПЛА X-47B, который успешно стартовал с авианосца ВМС США в 2011 году. Из рис. 3 видно, что уже было известно и принято считать, что детали АП могут иметь относительно шероховатые необработанные поверхности, а также поверхности для последующей ЧПУ-обработки.
Тот факт, что этот последний пункт многим может показаться логичным, что в равной степени относится к огромному разнообразию отливок, остается препятствием более пятнадцати лет спустя. Среди растущего числа компаний аэрокосмического сектора, которые являются новичками в области технологии АП и только начинают изучать возможности серийного производства, проблема шероховатости поверхности по-прежнему остается актуальной. Для многих лиц, принимающих решения, это остается источником сомнений в эффективности металлических деталей АП. Здесь предполагается, что причина кроется в наличии опубликованных примеров использования металлического АП в аэрокосмической промышленности. Таким образом, мы надеемся, что это описание одной из многих историй успеха, в которых детали металлического АП используются уже более десяти лет, уменьшит эти опасения: на детали X-47B действительно приходится значительное количество летных часов.
За годы, прошедшие после получения первого сертификата PBF-EB Ti-6Al-4V, Northrop Grumman сертифицировала множество компонентов в рамках нескольких авиационных и космических программ, и одним из последних стала сенсорная холодильная пластина, используемая в секторе систем управления полетами и производимый из сплава AlSi10Mg с помощью PBF-LB (рис. 4). Калеб Мартин (Caleb Martin), инженер-конструктор-механик, отметил:
“Гибкость, которую обеспечила АП, позволила нам разрабатывать, доводить до совершенства и поставлять холодильные плиты в четверть раза быстрее, чем при традиционном производстве”.
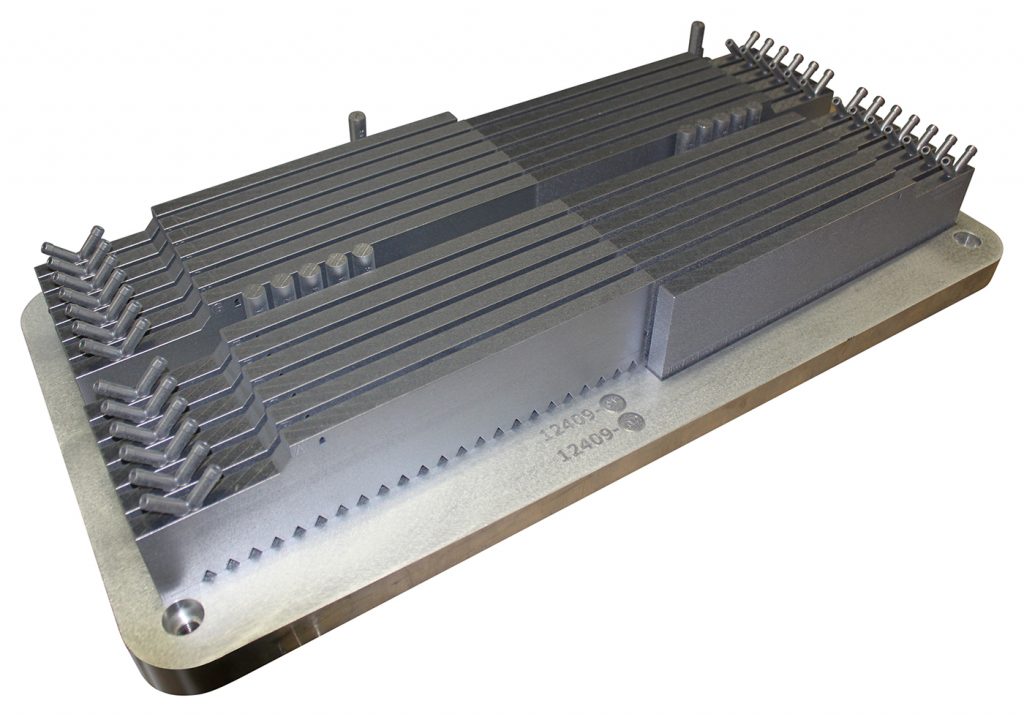
Рис. 4. Детали AlSi10Mg PBF-LB перед снятием с монтажной пластины (предоставлены Northrop Grumman)
В подтверждение того, как металлическое АП изменило цикл проектирования продукции, Northrop Grumman завершила разработку чертежей для этой детали в январе 2022 года и поставила функциональные образцы к августу 2022 года. С тех пор компания поставила шестнадцать таких сложных деталей, собранных в многофункциональные сборки, которые объединяют множество функциональных частей в одном датчике, уменьшая как количество необходимых отверстий, так и требования к размеру, весу и энергопотреблению, которые обычно связаны с такими расширенными возможностями.
Очевидно, что металлическое АП позволило Northrop Grumman быстро использовать технологию и для других программ, и адаптировать их к множеству возможностей, таких как многофункциональные реконфигурируемые интегрированные датчики с электронным сканированием (EMRIS). Эти критически важные устройства используются для одновременного выполнения функций радара, радиоэлектронной борьбы и связи. Это, пожалуй, первая компания, которая внедрила металлическое АП в жизненный цикл продукции и продолжает разрабатывать металлическое АП на различных платформах.
General Electric: Топливная форсунка и не только
Конечно, за эти 20 лет компания Northrop Grumman была не одинока в освоении металлического АП, и к настоящему времени все знакомы с широко известной топливной форсункой, изготовленной GE Aerospace для CFM International в двигателях LEAP 1A и 1B. Каждый из этих двигателей, которые в настоящее время популярны на нескольких узкофюзеляжных самолетах, использются топливные форсунки изготовленные с использованием АП, в зависимости от конкретной модели двигателя устанавливают комплекты по 18 и 19 таких форсунок.
CFM International, совместное предприятие GE Aerospace (США) и Safran (Франция), заявило, что топливные форсунки, изготовленные с применением АП, в пять раз долговечнее предыдущих моделей, что объясняется тем, что технология аддитивного производства позволила им создать более простую конструкцию с уменьшенным расходом топлива. Количество деталей в форсунке значительно сокращает объем пайки и сварки, необходимых для готовой сборки.
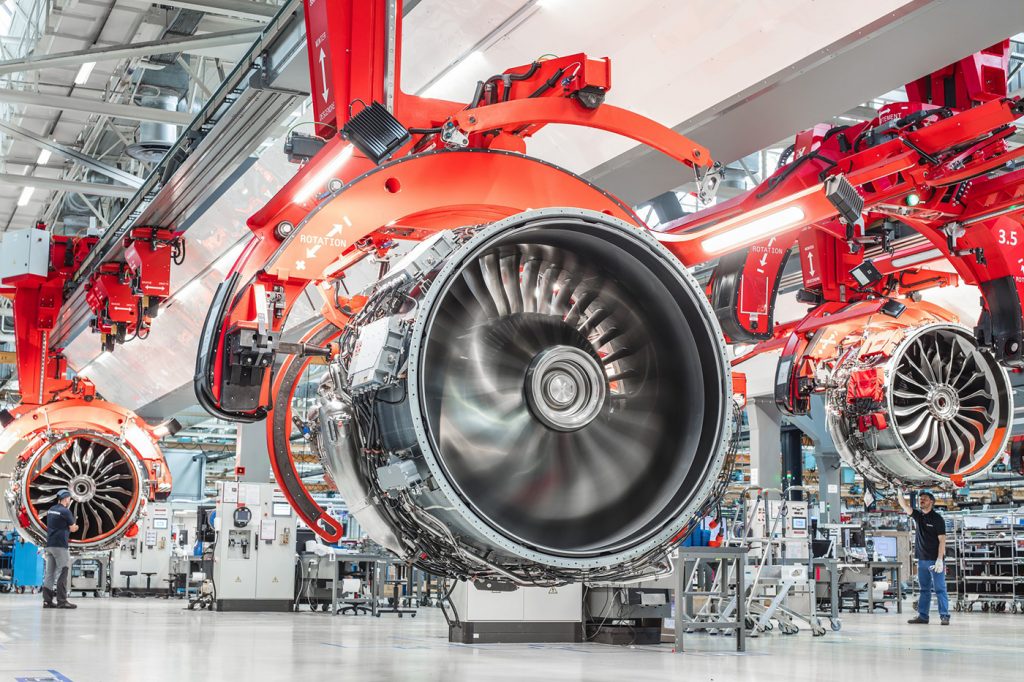
Рис. 5. Окончательная сборка двигателей LEAP на заводе Safran в Виллароше, Франция. Топливные форсунки GE Aerospace metal AM, используемые в двигателях, обеспечивают на 15% лучшую топливную экономичность по сравнению с двигателями предыдущего поколения, снижая общее воздействие коммерческих полетов на окружающую среду (фото Адриен Дасте/Safran).
Компания GE Aerospace взяла на себя ответственность за производство этой топливной форсунки, изготовленной с использованием PBF-LB и кобальт-хромового сплава, на своем заводе в Оберне, штат Алабама, где в 2015 году началось полномасштабное производство. В следующем году они поступили на службу и теперь используются на авиалайнерах Airbus A220, A320neo, A321neo, Boeing 737 MAX и COMAC C919. Сообщается, что топливная экономичность двигателей авиакомпаний на 15% выше, чем у двигателей предыдущего поколения, что снижает общее воздействие коммерческих рейсов на окружающую среду.
Летом 2021 года совместное предприятие объявило, что компания налетала 10 миллионов часов с использованием деталей металлического АП, и что на заводе в Оберне была изготовлена 100 000-я топливная форсунка с использованием АП. Ни в коем случае не будет преувеличением сказать, что это действительно знаменует собой первое массовое производство деталей для аэрокосмической промышленности с использованием технологии металлического АП. С 2019 года производительность составляет несколько сотен деталей в неделю, а также с учетом сокращения количества деталей до одной штучной детали, что является убедительным доказательством того, что металлическое АП было признано экономически выгодным методом производства.
GE Aerospace также участвовала в нескольких других проектах по разработке с использованием металлического АП и в настоящее время производит более 300 таких компонентов, для турбовентилятора GE9X, который был выбран Boeing для использования в своем авиалайнере 777X (рис. 6). Это последнее поколение авиационных двигателей включает в себя детали АП, которые были разработаны таким образом, чтобы объединить множество компонентов в единые конструктивные узлы, такие как топливные форсунки, теплообменники, корпуса датчиков, смеситель в камере сгорания и индуктор, а также используются для изготовления крупных ответственных деталей, таких как турбины низкого давления 5-й и 6-й ступеней и лопаток турбины низкого давления.

Рис. 6 В турбовентиляторе GE9X для изготовления деталей, включая топливные форсунки, теплообменники, корпуса датчиков, смесители в камерах сгорания, индукторы и лопатки турбин низкого давления 5-й и 6-й ступеней (предоставлены GE Aerospace), используется металл AM
Эти уникальные лопатки изготовлены из алюминида титана, выбранного за его исключительные характеристики при высоких температурах, и производятся компанией Avio Aero (приобретена GE в августе 2013 года) на ее заводе в Камери, Новара, Италия, с 2014 года. Используя технологию PBF-EB, на сегодняшний день Avio Aero изготовила все лопатки турбины низкого давления, необходимые для получения сертификата FAA для двигателя GE9X (получен в сентябре 2020 года), а также для поддержки процесса сертификации самолетов Boeing 777X.
Разработка этих лопаток TiAl для турбины низкого давления, как показано на рис. 7, также привела к тому, что они стали вдвое легче традиционных турбинных лопаток из никелевого сплава. Дэйв Эбботт (Dave Abbott) из GE Aerospace заявил:
“Для двигателя GE9X это означает снижение расхода топлива на 10% и, следовательно, снижение выбросов”.
Эбботт также рассказал о том, как аддитивное производство предоставило инженерам Avio Aero больше свободы творчества, что привело к изменению подхода к разработке новых конструкций и созданию более сложных компонентов.
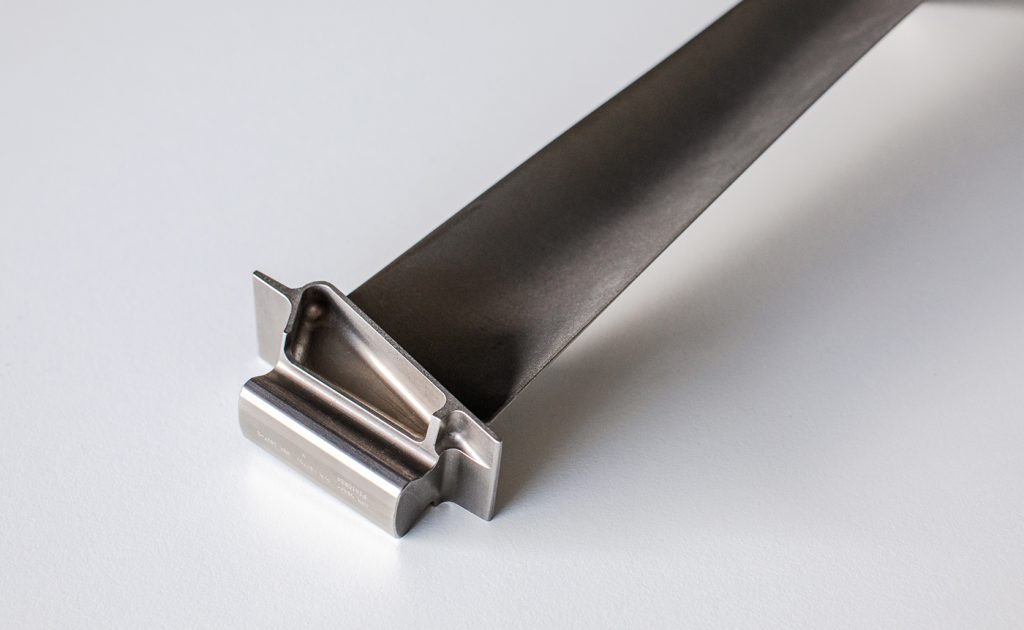
Рис. 7. Лопатка авиационной турбины Avio, изготовленная на станке Arcam PBF-EB и используемая в двигателе GE9X (фото компании компанией GE Additive)
Кроме того, новый турбовинтовой двигатель Catalyst, разработанный компанией GE Avio Aero, является первым, который был разработан, сконструирован и произведен с изначальным использованием деталей, изготовленных с применением АП. Этот двигатель был призван изменить правила игры в своем сегменте отрасли. С точки зрения производительности, GE представила двухступенчатые статорные лопатки, охлаждаемые лопатки турбины высокого давления и систему FADEC (Full Authority Digital Engine Control). Он обеспечивает лучшее в отрасли соотношение общего давления 16:1, что позволяет двигателю на 20% повысить топливную экономичность и на 10% увеличить крейсерскую мощность по сравнению с конкурирующими турбовинтовыми двигателями.
MTU Aero Engines
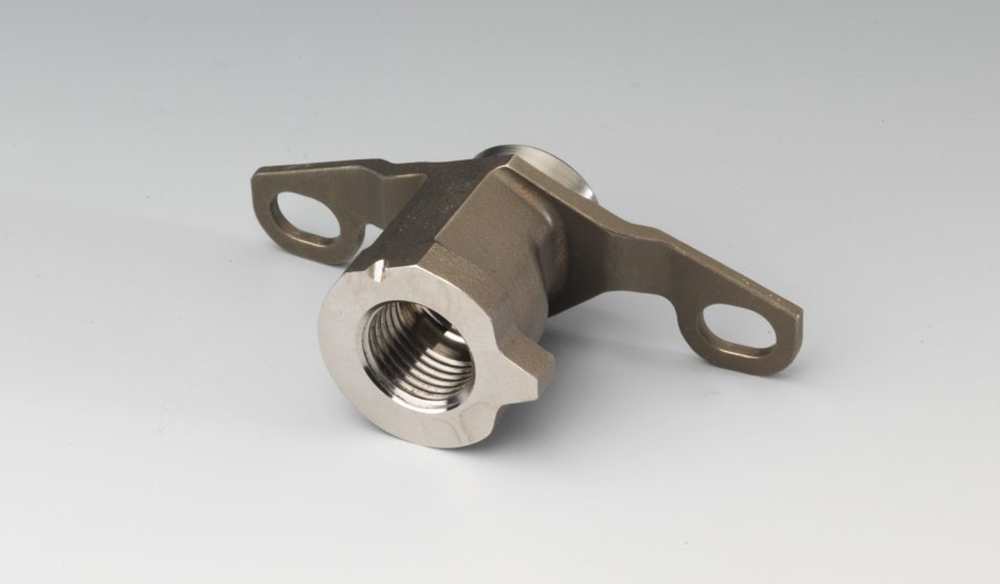
Рис. 8. Бороскопический патрубок, изготовленный компанией MTU Aero Engines на основе дополнительных компонентов для высокоскоростной турбины низкого давления редукторного турбовентиляторного двигателя PurePower® PW1100G-JM, который питает A320neo (фото компании MTU Aero Engines).
Компания MTU Aero Engines также занимает первое место в списке самых ранних. Она использовала технологию PBF-LB для изготовления бороскопической втулки для двигателя Pratt & Whitney PurePower PW1100G-JM, который работает на A320neo (рис. 8). Применение прорабатывалось в течение нескольких лет, прежде чем в 2013 году началось его производство.
Liebherr
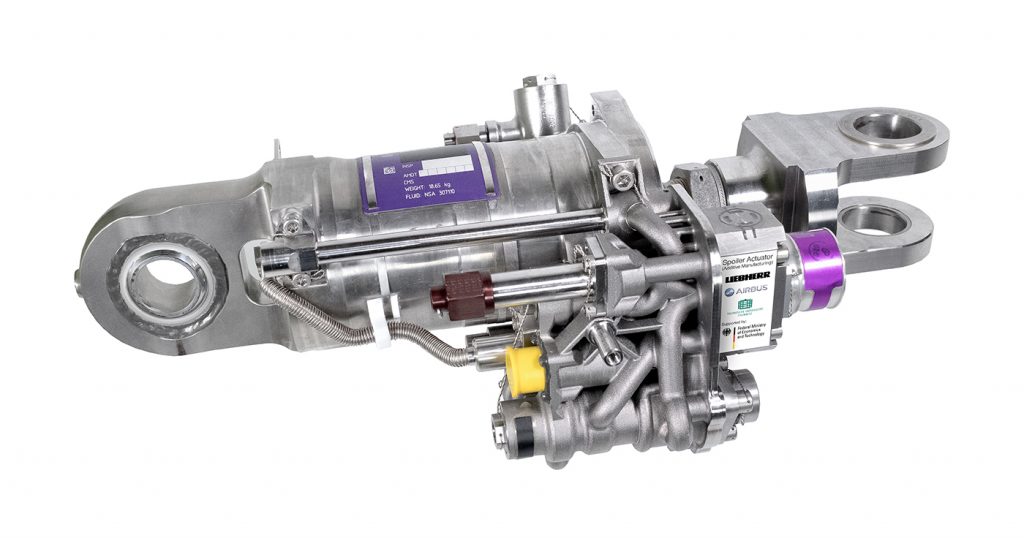
Рис. 9 Деталь PBF-LB системы управления приводом спойлера, используемой на Airbus A380 (фото компании Liebherr)
Менее известно, что Liebherr использовала PBF-LB для производства деталей управления полетом, используемых на Airbus A380. К сожалению, несмотря на то, что в долгосрочной перспективе сектор ТОИР, возможно, все еще планирует использовать AM для этого применения, снятие A380 с производства не приведет к массовому производству этих конкретных деталей (рис. 9). Компания также изготовила носовую опору шасси для A350 XWB, которая, как сообщается, стала первой деталью Airbus, прошедшей сертификацию для аддитивного производства из титана.
Airbus
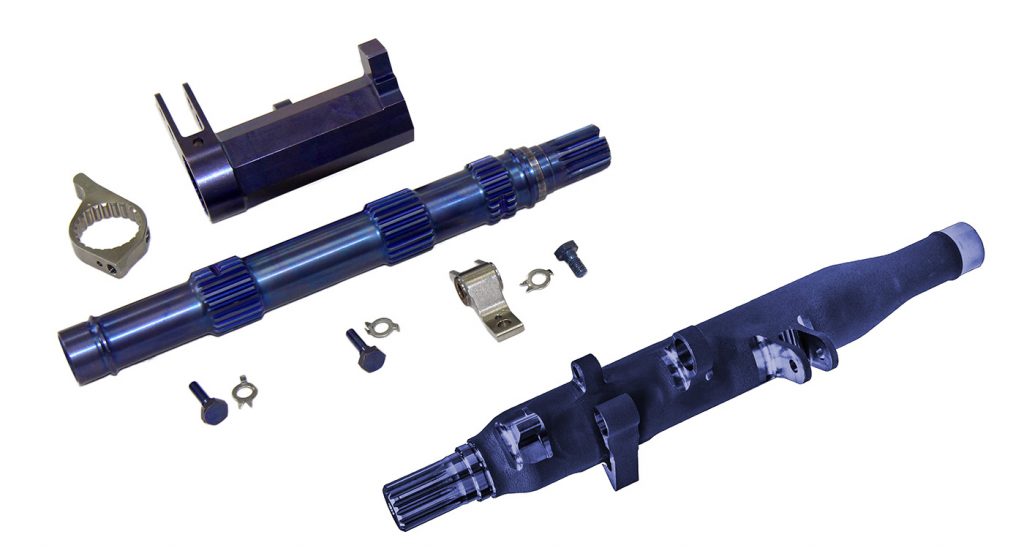
Рис. 10 Готовые металлические компоненты защелки (серебристого цвета) для A350 XWB (фото компании Airbus)
Дальнейшего успеха в металлическом АП добилась компания Airbus на своем самолете A350 XWB, которая с 2019 года использует технологию аддитивного производства металла для изготовления стержня дверной защелки и других компонентов. Благодаря собственной внутренней цепочке поставок, запчасти производятся дочерней компанией Airbus Helicopters в Донауверте, Германия. Изготавливаемые из Ti-6Al-4V партиями по 28 штук одновременно, на данный момент изготовлено более 1000 деталей с использованием мультилазерного PBF-LB, и недавно начали устанавливать их на пассажирские самолеты, находящиеся в эксплуатации (рис. 10). Филипп Эмиль, эксперт по аддитивному производству в Airbus во Франции, отметил:
“3D-Печатные стержни защелок на 45% легче и на 25% дешевле в производстве, чем традиционные”.
Safran
Каждый из совладельцев CFM International по отдельности продолжал изучать и развивать производство металлоконструкций в рамках своей группы компаний, как и большинство других значимых игроков отрасли. На сегодняшний день металлическое АП интегрировано в значительное число циклов разработки продуктов и производства. В 2019 году компания Safran Aero Boosters объявила, что с 2015 года работает над альтернативой литому корпусу для блока смазки, предназначенного для использования в двигателе LEAP, и оптимизированного для АП. Компания Safran Aero Boosters изготовила новые детали из того же алюминиевого сплава F357, что и исходная отливка, и достигла показателя TRL 6 с помощью PBF-LB, когда один из узлов смазки впервые был использован на двигателе LEAP-1A. Однако, в отличие от GE Aerospace, Safran в то время не располагала собственными производственными мощностями и вместо этого решила развивать внешнюю цепочку поставок, доверив производство деталей внешним поставщикам услуг металлического АП.
Collins Aerospace
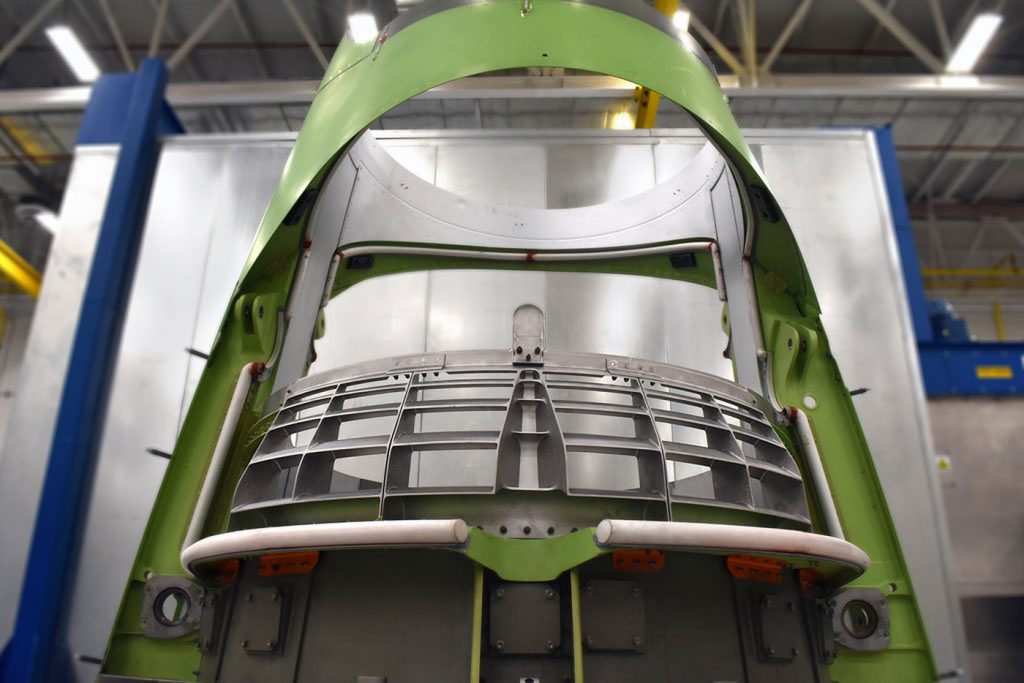
Рис. 11 Каскадная решетка реверсора тяги, изготовленная с использованием АП(фото компании Collins Aerospace)
Компания Collins Aerospace, входящая в группу RTX, также активно применяла АП, и на сегодняшний день выпустила более 75 различных деталей. Являясь крупным поставщиком первого уровня, компания имеет возможность найти множество различных применений для АП, и ее успехи включают в себя детали для терморегулирования, двигателя, гондолы, а также различные сопла, корпуса и датчики. Компания Collins сообщает, что благодаря применению принципов, лежащих в основе “Дизайна для АП”, в настоящее время достигается регулярная экономия веса на 10-30% при соответствующем сокращении количества деталей на 50-80%. Возможно еще более важно то, что компания добилась сокращения сроков изготовления на 60-80%. Одним из ее ключевых успехов стала крупная каскадная система реверсирования тяги, изготовленная на основе аддитивных технологий, в гондоле бизнес-джета (рис. 11).
Rolls Royce
Хотя компания Rolls-Royce еще не объявила о массовом использовании металлического АП, в 2015 году она объявила, что успешно изготовила большой титановый корпус переднего подшипника для двигателя Trent XWB-97. Эта конструкция диаметром 1,5 метра, собранная из нескольких металлических деталей АП PBF-EB, на тот момент была самой большой несущей конструкцией, которая когда-либо устанавливалась на коммерческий авиалайнер, когда она использовалась в испытательном полете Airbus A350.
Хотя этой детали так и не суждено было попасть в серийное производство, она доказала, что АП способно производить детали, имеющие решающее значение для безопасности. Постоянная оценка технологий АП придала Rolls-Royce уверенности в продолжении разработки деталей для двигателя UltraFan® следующего поколения. Результаты этого исследования еще не опубликованы, но аналогичная деталь, изготовленная с помощью АП, станет еще более мощной, чем та, что используется в Trent XWB-97.
Rolls-Royce также сотрудничает со своими партнерами по поставкам в Испании, компанией ITP Aero. Существует вероятность того, что новый двигатель будет включать в себя корпус хвостового подшипника, изготовленный тем же образом, который уже использовался в демонстрационном двигателе, который, предположительно, был собран и испытан в Дерби в прошлом году (рис. 12). Являясь ключевым конструктивным элементом, корпус хвостового подшипника спроектирован таким образом, чтобы выдерживать эксплуатационные нагрузки в любых условиях. Часть подшипников, которые поддерживают вал вентилятора, основной двигательной установки двигателя, встроены в корпус, равно как и съемные шумоглушающие панели, они также были изготовлены с помощью АП для демонстрационного двигателя.
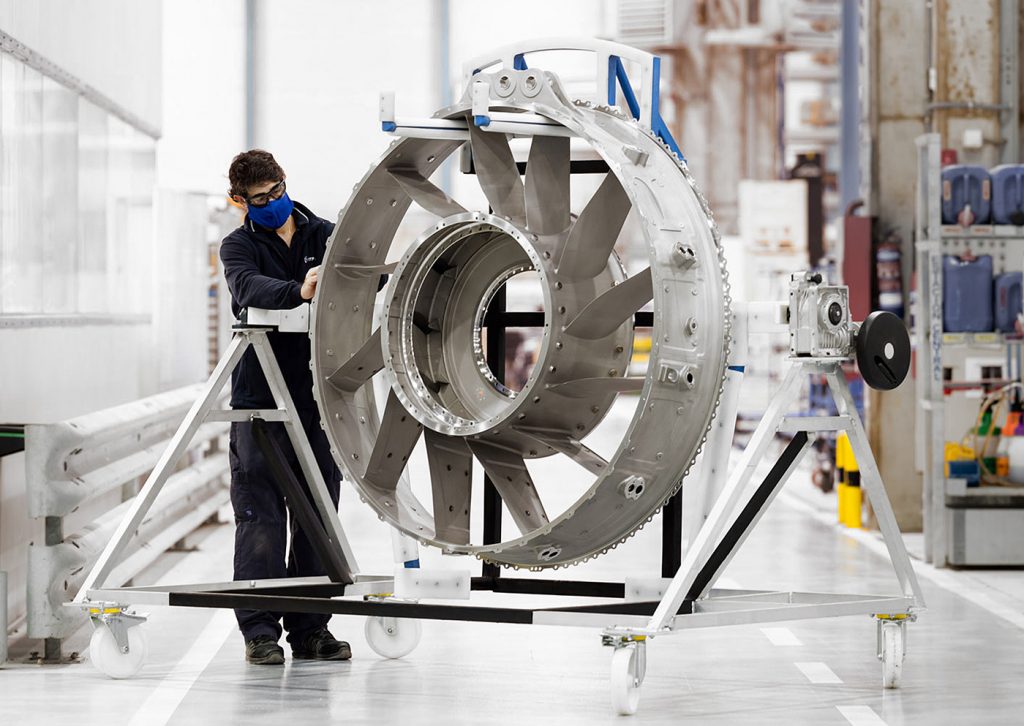
Рис. 12 Корпус хвостового подшипника, использованный в первом демонстрационном двигателе Rolls-Royce Ultra Fan® (фото ITP Aero)
Среди других недавних разработок Rolls-Royce – специально изготовленная камера сгорания с низким уровнем выбросов для двигателя Pearl 10X, который был разработан для бизнес-джета Falcon 10X компании Dassault. Эта деталь была изготовлена на мультилазерной системе PBF-LB и состоит из АП-плиток, которые затем собираются для формирования корпуса камеры сгорания. Преимущество, которое, как утверждается, получила компания Rolls-Royce, связано с тем, что камеры сгорания предыдущих двигателей изготавливались методом литья, в которых требовалось просверливать отверстия для охлаждения. АП предоставило больше свободы в проектировании необходимых отверстий непосредственно в каждом компоненте, которые можно было полностью оптимизировать для подачи охлаждающего воздуха, необходимого для работы камеры сгорания. Что касается производительности, то утверждается, что новая конструкция имеет меньшее количество температурных точек перегрева, что повышает мощность турбины высокого давления двигателя, что, в свою очередь, должно привести к повышению топливной экономичности при одновременном снижении выбросов оксидов азота.
Объединенная Двигателестроительная Корпорация
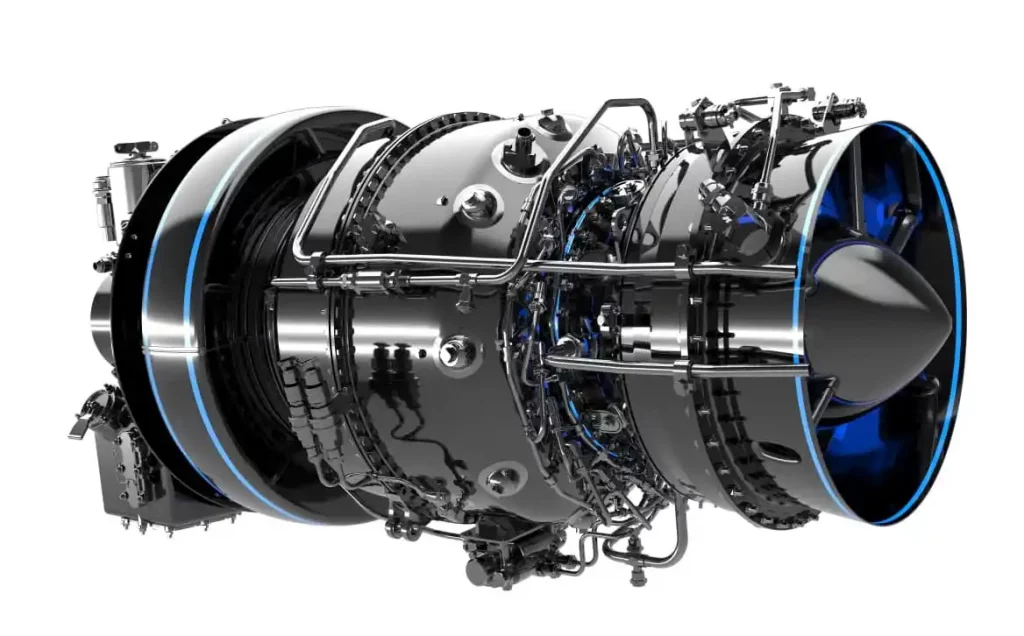
Рис. 13 Объединенная двигателестроительная корпорация (ОДК), Москва, намерена производить до 70% вертолетного двигателя ВК-1600В с использованием аддитивного производства (фото компании ОДК)
Разработка двигателей с использованием АП уже стала мировым приоритетом. Объединенная двигателестроительная корпорация (ОДК), базирующаяся в Москве, объявила, что намерена производить до 70% двигателя ВК-1600В, своего первого полностью 3D-смоделированного двигателя, с использованием аддитивного производства (рис. 13). Этот двигатель будет использоваться на вертолете Ка-62, и в сочетании с другими компонентами планера, по словам компании, около 10% всего вертолета Ка-62 будет производиться с помошью АП. Сообщалось, что ВК-1600В планируется ввести в эксплуатацию в 2023 году, а массовое производство металлических деталей AM начнется в 2024 году.
Eaton
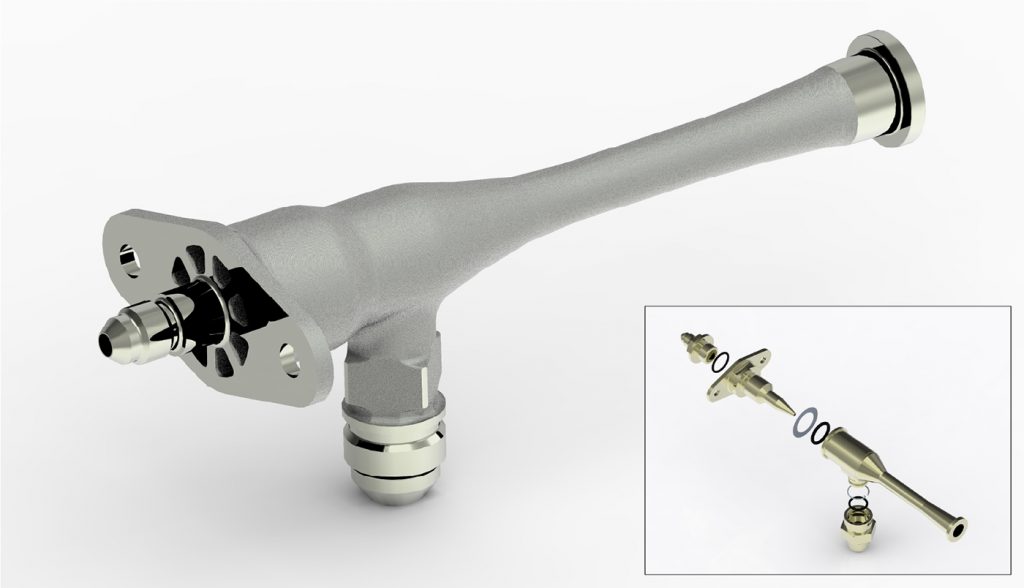
Рис. 14. Струйный насос для продувки топлива, изготовленный на основе АП, и на вставке – увеличенный вид насоса обычного производства (фото компании Eaton Aerospace)
В других частях широко распространенной цепочки поставок аэрокосмического сектора поставщики важнейших комплектующих, такие как Eaton, развивают свои собственные возможности в области АП. На протяжении ряда лет компания разрабатывала технологические процессы АП с использованием титана, инконеля, нержавеющих сталей и алюминиевых сплавов, а недавно совместно с Airbus разработала внутреннюю квалификационную базу для производства струйных насосов Eaton для продувки топлива с использованием технологии PBF-LB (рис. 14). Этот процесс также должен был продемонстрировать, что новые насосы Eaton будут работать в соответствии с оригинальными спецификациями компонентов, требованиями заказчика и стандартами летной годности EASA и FAA.
Майк Йорк, директор AM и Digital Engineering в Eaton, сказал:
“Eaton Aerospace использует возможности АП для производства превосходных продуктов и системных решений для наших клиентов, что приведет к увеличению доли рынка. Кроме того, мы использовали эту технологию для значительного снижения веса, количества необходимых компонентов и сборки, что привело к значительной экономии эксплуатационных расходов”.
После продолжительного квалификационного периода струйный насос для откачки топлива Eaton, изготовленный на основе АП, был одобрен EASA для коммерческих полетов и сегодня находится в эксплуатации. Благодаря использованию АП компания не только снизила вес насоса на 30%, но и сократила время сборки компонентов и устранила потенциальные пути утечки, такие как уплотнения и резьбовые соединения, в результате объединения одиннадцати деталей в единую деталь (рис. 14).
Продолжая свою многолетнюю деятельность в области литья и механической обработки, компания Eaton в настоящее время внедряет технологию АП во все сферы бизнеса в дополнение к существующим производственным процессам, а также использует другие аддитивные технологии, такие как холодное напыление, для улучшения возможностей ремонта старых и более уникальных деталей для клиентов на вторичном рынке.
“Эти примеры показывают, что авиакосмические компании и цепочка поставок в настоящее время активно работают вместе над внедрением решений мет аллического АП, и в будущем мы увидим еще больше подобных решений”, – добавил Йорк.
Возможности прямого энергетического осаждения (DED)
Прямое энергетическое напыление включает в себя широкий спектр технологий АП, которые позволяют расплавлять проволоку или металлические порошки для эффективного формирования 3D-объектов путем наложения сварных швов слой за слоем. Преимущество DED заключается в высокой скорости напыления как на платформе, так и непосредственно на уже существующих деталях. Это делает данную группу технологий АП особенно подходящей для ремонта и производства крупногабаритных изделий.
Однако, несмотря на то, что это одна из старейших технологий АП, впервые разработанная в 1980-х годах в качестве лазерной наплавки, в массовое производство она внедрялась реже. Вместо этого доминирующим направлением применения технологии стал ремонт, особенно в процессах лазерного напыления, разработанных такими компаниями, как Trumpf и Optomec. Последние утверждают, что во многих странах они установили сотни систем с сертифицированными процессами ремонта лопаток турбин с использованием DED, и на сегодняшний день было произведено огромное количество ремонтов, возможно, десятки миллионов. Вместо этого аэрокосмический сектор в наибольшей степени использует проволочные технологии для создания новых производств, и несколько компаний разрабатывают продукты и процессы.
Norsk Titanium и Boeing
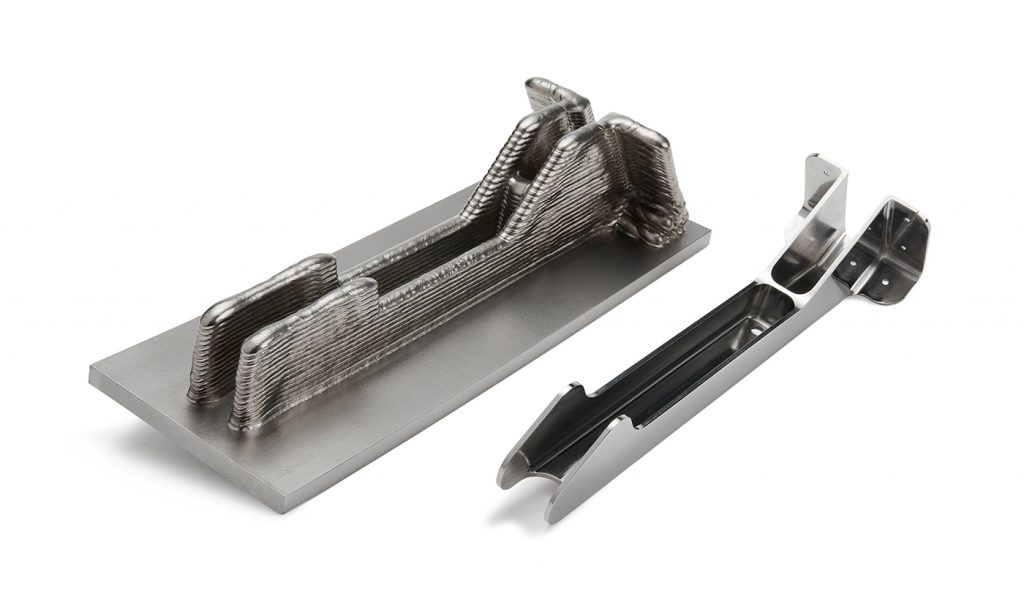
Рис. 15 Конструктивные элементы DED Ti-6Al-4V в наплавленном и обработанном состоянии, изготовленные в больших объемах для Boeing 787 Dreamliner компанией Norsk Titanium (фото компании Boeing)
Сообщается, что норвежская Norsk Titanium стала первой компанией, получившей разрешение FAA на производство компонентов АП с использованием DED в 2017 году. Это стало следствием того, что Boeing получил задание изготовить детали для самолета 787 Dreamliner (рис. 15).
Журнал Metal AM magazine недавно побеседовал с Мэтью Криллом, младшим техническим сотрудником в области АП в Boeing, чтобы узнать больше о результатах исследования, которое было опубликовано в январе 2018 года. Крилл объяснил, что по мере того, как АП начало набирать обороты в этом секторе, Boeing обратился к своим поставщикам за решением для диагонального крепления пассажирского салона Boeing 787. Каждый комплект состоит из четырех деталей, и компания Norsk Titanium стала ее квалифицированным поставщиком, а успех в отрасли был отмечен в 2018 году премией Aviation Week Network 2018 за первые конструкционные титановые детали АП, которые были включены в состав каждого коммерческого самолета.
Эти детали были установлены на первый самолет в июне 2017 года и с тех пор находятся в серийном производстве. Крилл заявил:
“Несмотря на то, что многие стремились радикально изменить конструкцию, эта деталь намеренно сохранила ту же конечную геометрию, независимо от того, была ли она изготовлена из листа или из заготовки, она отлично подошла для наплавки проволокой”.
Для Boeing основной упор был сделан на снижение затрат и повышение экологичности. Развивая этот успех, Boeing внедрила несколько других деталей, изготовленных с использованием технологии Norsk Titanium, и все они были установлены по программе 787 через своих субподрядчиков.
Крилл добавил: “Доказанные преимущества были получены благодаря типичному снижению на 80% коэффициента «купить-вылететь» при сравнении обработки детали из почти чистой преформы с обработкой из пластины. Такое снижение дает преимущества с точки зрения стоимости детали и экологичности за счет сокращения выбросов”.
Пожалуй, наиболее полное исследование и разработка DED были проведены NASA, и такие эксперты, как Пол Грэдл, старший инженер-двигателестроитель Центра космических полетов имени Маршалла в NASA, часто представляли и публиковали свои результаты. Однако, несмотря на ошеломляющий объем исследований и разработок, информация о запущенных компонентах, используемых NASA в миссиях, ограничена.
Решения для спутников и антенн
Более того, в космическом секторе аддитивное производство стало почти нормой. Если оставить в стороне ракетные двигатели как самостоятельную тему, то компоненты, которые регулярно производятся, включают клапаны окислителя в двигателях Merlin 1D, используемых на ракетах SpaceX Falcon 9, двигатели Super Draco, которые обеспечивают отказоустойчивую двигательную установку для аварийной системы ракетной капсулы SpaceX Dragon 2, а также турбины, поставленные компанией GKN для Ariane Group для двигателя Prometheus на Ariane 6. NSAS также было в авангарде внедрения технологии АП, и марсоход Perseverance, отправленный на Марс, он имеет 11 металлический компонентов изготовелнных с помощью АП, используемых в двух его приборах.
Однако аддитивное производство металлов впервые было применено в менее сложных космических условиях, а сплав AlSi10Mg использовался в нескольких спутниковых программах. В этих случаях именно цепочка поставок, по-видимому, наилучшим образом отреагировала на использование АП в этих передовых областях применения, поставляя Airbus Defence and Space (AD&S) различные пассивные конструктивные и активные коммуникационные устройства. Британская компания заключила контракт с внешними поставщиками услуг АП на производство таких деталей, как широко разрекламированный антенный кронштейн TMTC, который с 2015 года, вероятно, является первой полностью готовой деталью, которая будет использоваться при запуске спутников Eurostar E3000, а совсем недавно – более 500 компонентов радиочастотного волновода для двух спутников Eurostar Neo-спутники серии HOTBIRD 13F и 13G. Все эти спутниковые программы были успешно запущены до 2022 года для поддержки телевизионных ретрансляционных услуг Eutelsat в Европе, на Ближнем Востоке и в Северной Африке. Кронштейн TMTC стал знаковым моментом для компании, поскольку он позволил снизить вес на 35% и упростил конструкцию предыдущего кронштейна, который состоял из 4 частей и 44 заклепок, а теперь это один элемент. Однако, применив программное обеспечение и генеративный дизайн, компания также смогла изготовить деталь, которая была на 40% жестче, чем предыдущий изготовленный компонент.
Приведенный выше пример сам по себе является достаточным доказательством готовности формирующейся цепочки поставок в сфере аддитивного производства к удовлетворению потребностей аэрокосмического сектора. Сюда входят такие компании, как Optisys, которая разработала целый ряд продуктов с помощью АП (рис. 16). Директор по инновациям Роб Смит (Rob Smith) заявил, что они увидели все эти преимущества благодаря внедрению АП, “быстрому переходу к разработке и производству нестандартных комбинаций и вариантов монтажа. Кроме того, мы можем создавать гораздо более компактные компоновки, которые имеют меньший вес, более высокую надежность за счет сокращения количества деталей и более стабильной производительности”.
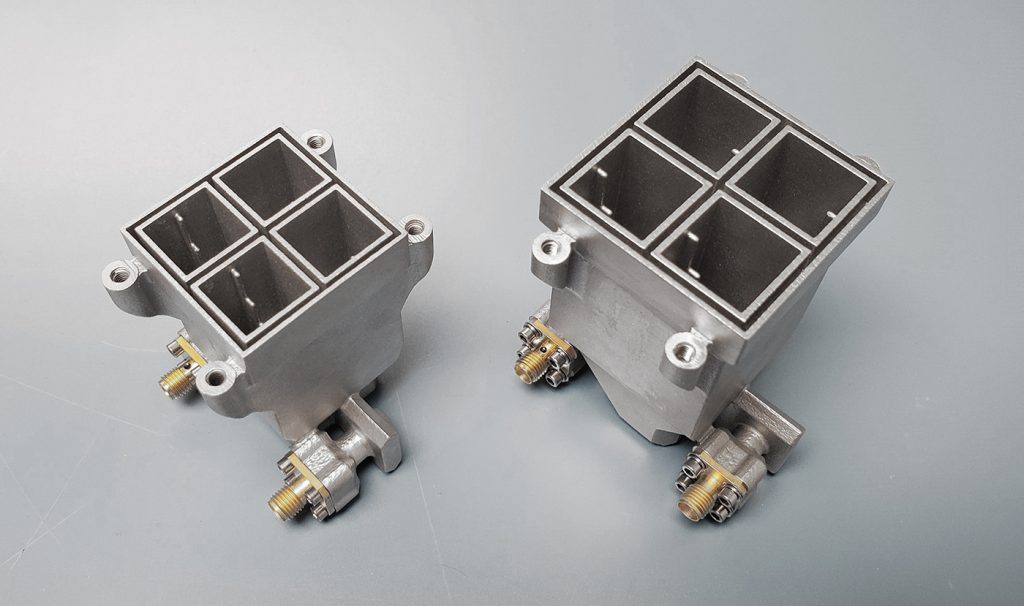
Рис. 16 Детали радиочастотной антенны, изготовленные с помошью PBF-LB для использования на низкой околоземной орбите (фото Optisys)
Компания разрабатывает решения для АП-антенн с 2016 года и уже поставила более сорока космических компонентов различным заказчикам, в основном для использования на низкой околоземной орбите. Некоторые компоненты были включены в программы успешных запусков, например, компоненты рупорной антенной решетки, доставленные на Международную космическую станцию (МКС) в ноябре 2018 года, и несколько других коммерческих спутниковых программ, рассчитанных до 2022 года.
Компания разрабатывает эти детали исключительно с использованием технологии АП в качестве основного производственного процесса и добилась значительного повышения производительности. По сравнению с одним из известных устройств, вес которого составлял 4-5 кг, теперь они могут обеспечить эквивалентную функциональность устройства весом всего 40-50 г. Даже самые типичные конструкции оказали огромное влияние, и Смит сказал: “По моим представлениям, мы снижаем вес в среднем на 50-80%”. Наибольшая экономия веса достигается за счет существенного сокращения количества деталей и отказа от винтов, шайб и переходников. Он добавил: “Я бы сказал, что мы довольно часто заменяем в соотношении 100:1 в наших сетях пассивных волноводов, и во многих случаях наши результирующие конструкции просто невозможно создать с помощью традиционных процессов”.
Это отрасль, которая действительно выигрывает от возможности массовой кастомизации без необходимости изменения каких-либо производственных процессов. В примере с Optisys, показанном на рис. 16, компания смогла создать линейку продуктов, в которой детали похожи, но работают с несколько иной частотой. Обычно для этого требуются значительные изменения в традиционных конструкциях и производстве деталей. Кроме того, значительно сокращается время изготовления. Хотя большая часть его времени уходит на проверку конструкции, что характерно не только для процессов АП, он работает с меньшим количеством деталей, что означает значительное сокращение этапов проектирования, документации, выпуска и сборки. Благодаря своему уникальному подходу компания утверждает, что может поставлять запчасти в критические сроки, чего другие просто не могут сделать.
Говоря о настройке и сроках поставки, Смит заключает: “Наш производственный процесс всегда одинаков, и таким образом мы можем добиться хорошей настройки с помощью цифрового производства…. мы разработали дизайн всего за две недели, что совершенно неслыханно в нашей отрасли, но, как правило, я бы сказал, что мы сокращаем сроки с нескольких лет до шести-девяти месяцев”.
Вывод
Примеры, приведенные здесь, предоставлены некоторыми из ведущих компаний аэрокосмического сектора, но есть и множество других примеров, которые можно найти в статьях и пресс-релизах по всему интернету. 20 лет назад об этом можно было бы рассказать очень коротко, а сегодня этому можно посвятить целую книгу.
Аддитивное производство из металлов ввело аэрокосмическую отрасль в новую эру свободы дизайна, легких конструкций и улучшенных эксплуатационных характеристик. Успешное применение технологий Powder Bed Fusion, Directed Energy Deposition и – несомненно, очень скоро – Binder Jetting не просто нарушило статус-кво, а произвело революцию в возможности производства более функциональных деталей с более сложной геометрией для повышения топливной эффективности, снижения выбросов и увеличения долговечности.
По мере того как аэрокосмический сектор продолжает изучать возможности металлического АП на протяжении всей цепочки создания стоимости своих деталей, будет происходить непрерывное развитие способов подготовки файлов сборки, моделирования для компенсации короблений, оптимизации траекторий движения инструмента, повышения устойчивости обработки и переработки материалов, а также стандартизации последующей обработки, контроля, квалификации и сертификации.
Все это подкрепляется параллельной разработкой столь необходимых промышленных стандартов такими организациями, как ISO, ASTM и SAE International. Все они имеют целенаправленные рабочие группы, занимающиеся разработкой документированных требований к процессам, материалам и деталям, которые могут быть использованы в производстве аэрокосмической продукции, а ISO и ASTM объединили свои усилия для разработки некоторых опубликованных стандартов. На сегодняшний день ASTM, возглавляемый комитетом F42, опубликовал три стандарта, направленных на квалификацию станков, квалификацию операторов и классификацию деталей, специально применяемых в аэрокосмическом секторе.
Еще четыре стандарта находятся на разных стадиях разработки. Аналогичным образом, основной отраслевой орган по стандартам в данном секторе, SAE International, также имеет свои рабочие группы ASM AM – Metals. Несмотря на то, что SAE немного запоздала с разработкой стандартов для производства аэрокосмических деталей, с 2016 года она опубликовала в общей сложности 33 стандарта и рекомендуемые практики. За ними следуют еще 36 документов, над которыми в настоящее время ведется работа, а полдюжины или более близки к публикации в конце этого года. Они охватывают все: состав и физические свойства металлических порошков и проволоки, минимальные требования к технологическому процессу и специальную документацию, и даже требования к мониторингу и повторной квалификации переработки и повторного использования исходных материалов.
Кроме того, будущее аддитивного производства металлов гарантировано, поскольку такие организации, как FAA (в США) и EASA (в Европе), работают вместе, чтобы обеспечить надежную основу для сертификации летной годности деталей АП. На недавней встрече в Кельне (Германия) этих организаций, которые уже несколько лет проводят совместную конференцию по АП, было подчеркнуто, что мониторинг на месте должен стать ключевой областью, которую должны развивать как производители систем, так и пользователи. Рабочая группа «Разработка пятилетнего плана по допуску EASA/FAA – мониторинг машин», уже третий год подряд занимается разработкой мер, которые позволят цепочке поставок пройти критерии допуска FAA/EASA. Это в значительной степени бросает вызов всем OEM-производителям промышленных 3D-принетров; они должны ответить на это, продвинув свои технологии дальше уровня простого сбора данных о процессе построенияи превратив их в полноценные отчеты о построении, которые гарантируют качество деталей.